Batching process of antibacterial BOPA film production raw materials
A batching process and raw material technology, applied in the field of batching technology of raw materials for the production of antibacterial BOPA film, can solve the problems of error, low work efficiency, long batching time, etc.
- Summary
- Abstract
- Description
- Claims
- Application Information
AI Technical Summary
Problems solved by technology
Method used
Examples
Embodiment Construction
[0018] Below in conjunction with the examples, the specific implementation of the present invention will be further described in detail. The following examples are used to illustrate the present invention, but are not intended to limit the scope of the present invention.
[0019] A kind of batching process of antibacterial BOPA film production raw material of the present invention comprises the following steps: (1), raw material screening: calcium carbonate and talcum powder are screened;
[0020] (2), weighing of raw materials: put polyamide 6 into a measuring tank for weighing, put calcium carbonate into a measuring tank for weighing, put talcum powder into a measuring tank for weighing, put the fat The family amide wax is put into the metering tank and weighed;
[0021] (3) Oscillating feeding: Take the weighed polyamide 6, calcium carbonate, talcum powder and aliphatic amide wax and add them to the stirring tank. The pipe is knocked and oscillated;
[0022] (4), raw mat...
PUM
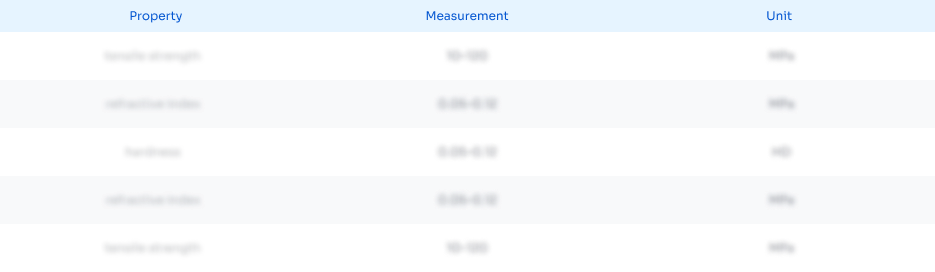
Abstract
Description
Claims
Application Information

- R&D Engineer
- R&D Manager
- IP Professional
- Industry Leading Data Capabilities
- Powerful AI technology
- Patent DNA Extraction
Browse by: Latest US Patents, China's latest patents, Technical Efficacy Thesaurus, Application Domain, Technology Topic, Popular Technical Reports.
© 2024 PatSnap. All rights reserved.Legal|Privacy policy|Modern Slavery Act Transparency Statement|Sitemap|About US| Contact US: help@patsnap.com