Support film for OLED module and preparation method thereof
A technology of supporting film and module, applied in the field of supporting film of OLED module and its preparation, can solve problems such as cohesion of adhesive layer, insufficient stiffness, easy deformation, etc., achieve low tearing film static voltage, and improve folding performance , the effect of high cohesion
- Summary
- Abstract
- Description
- Claims
- Application Information
AI Technical Summary
Problems solved by technology
Method used
Image
Examples
Embodiment 1
[0055] This embodiment provides a support film for an OLED module, which consists of a 50 μm antistatic PET substrate layer, a 7 μm antistatic polyurethane pressure-sensitive adhesive layer, a 75 μm double-sided antistatic PET substrate layer, and a 25 μm antistatic PET substrate layer arranged sequentially from top to bottom. Polyacrylate pressure-sensitive adhesive layer and 50μm double-sided antistatic PET release film layer.
[0056] In parts by weight, the raw material composition of the antistatic polyurethane pressure-sensitive adhesive layer includes: 100 parts of low-viscosity polyurethane adhesive (U-1401, Lion King of Japan), 0.4 part of bistrifluoromethanesulfonylimide lithium salt solution ( CF1101C, Guotai Chaowei), 10 parts of modified polyisocyanic acid (hardener N, Japan Lion King) and 150 parts of ethyl acetate. The polyurethane adhesive composition is mechanically stirred, coated on the non-antistatic surface of 50 μm antistatic PET (ST, Yangzhou Wanrun), an...
Embodiment 2
[0060] This embodiment provides a support film for an OLED module, which consists of a 50 μm antistatic PET substrate layer, a 7 μm antistatic polyurethane pressure-sensitive adhesive layer, a 75 μm double-sided antistatic composite film layer, and a 25 μm poly Acrylic pressure-sensitive adhesive layer and 50μm double-sided antistatic PET release film layer.
[0061] In parts by weight, the raw material composition of the antistatic polyurethane pressure-sensitive adhesive layer includes: 90 parts of low-viscosity polyurethane adhesive (U-1401, Lion King of Japan), 0.4 part of bistrifluoromethanesulfonylimide lithium salt solution ( CF1101C, Guotai Chaowei), 8 parts of modified polyisocyanic acid (hardener N, Japan Lion King) and 150 parts of ethyl acetate. The polyurethane adhesive composition is mechanically stirred, coated on the non-antistatic surface of 50 μm antistatic PET (ST, Yangzhou Wanrun), and after being cured in an oven, it is pasted on a 50 μm PET release film (...
Embodiment 3
[0066] This embodiment provides a support film for an OLED module, which consists of a 50 μm antistatic PET substrate layer, a 7 μm antistatic polyurethane pressure-sensitive adhesive layer, a 75 μm double-sided antistatic PET substrate layer, and a 25 μm antistatic PET substrate layer arranged sequentially from top to bottom. Polyacrylate pressure-sensitive adhesive layer and 50μm double-sided antistatic PET release film layer.
[0067] In parts by weight, the raw material composition of the antistatic polyurethane pressure-sensitive adhesive layer includes: 85 parts of low-viscosity polyurethane adhesive (U-1401, Lion King of Japan), 2 parts of bistrifluoromethanesulfonylimide lithium salt solution ( CF1101C, Guotai Chaowei), 5 parts of modified polyisocyanic acid (hardener N, Japan Lion King) and 150 parts of ethyl acetate. The polyurethane adhesive composition is mechanically stirred, coated on the non-antistatic surface of 50 μm antistatic PET (ST, Yangzhou Wanrun), and a...
PUM
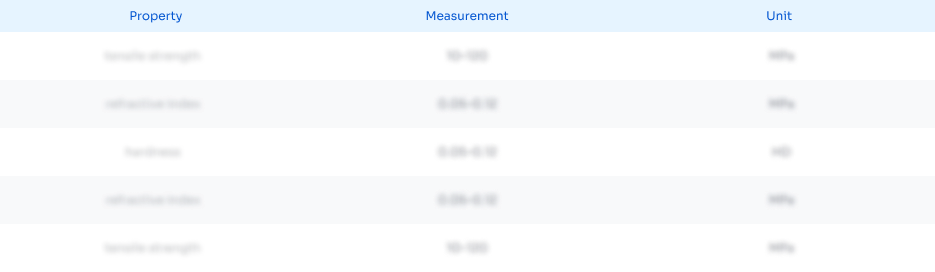
Abstract
Description
Claims
Application Information

- R&D
- Intellectual Property
- Life Sciences
- Materials
- Tech Scout
- Unparalleled Data Quality
- Higher Quality Content
- 60% Fewer Hallucinations
Browse by: Latest US Patents, China's latest patents, Technical Efficacy Thesaurus, Application Domain, Technology Topic, Popular Technical Reports.
© 2025 PatSnap. All rights reserved.Legal|Privacy policy|Modern Slavery Act Transparency Statement|Sitemap|About US| Contact US: help@patsnap.com