Seven-degree-of-freedom double-module parallel cooperative robot for 3C assembly
A degree of freedom, dual-module technology, applied in manipulators, program-controlled manipulators, manufacturing tools, etc., can solve problems such as complex installation, lack of dexterity and precision, and obstacles to the application of assembly robots
- Summary
- Abstract
- Description
- Claims
- Application Information
AI Technical Summary
Problems solved by technology
Method used
Image
Examples
Embodiment Construction
[0030] The concept, specific structure and technical effects of the present invention will be clearly and completely described below in conjunction with the embodiments and the accompanying drawings, so as to fully understand the purpose, solutions and effects of the present invention. It should be noted that the embodiments in the present application and the features of the embodiments may be combined with each other in the case of no conflict.
[0031] It should be noted that, unless otherwise specified, when a feature is called "fixed" or "connected" to another feature, it can be directly fixed or connected to another feature, or it can be indirectly fixed or connected to another feature. on a feature. In addition, the descriptions of upper, lower, left, right, top, bottom, etc. used in the present invention are only relative to the mutual positional relationship of each component of the present invention in the accompanying drawings.
[0032] Also, unless otherwise define...
PUM
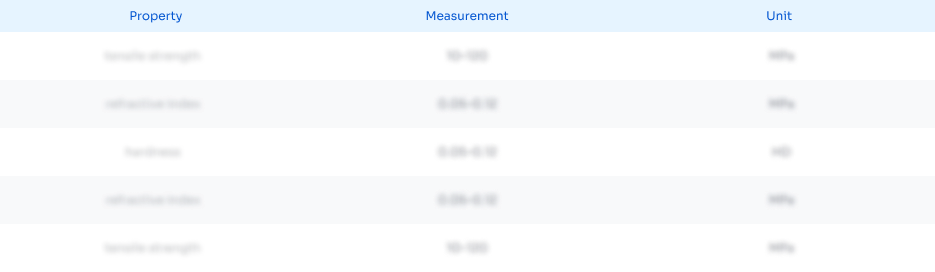
Abstract
Description
Claims
Application Information

- Generate Ideas
- Intellectual Property
- Life Sciences
- Materials
- Tech Scout
- Unparalleled Data Quality
- Higher Quality Content
- 60% Fewer Hallucinations
Browse by: Latest US Patents, China's latest patents, Technical Efficacy Thesaurus, Application Domain, Technology Topic, Popular Technical Reports.
© 2025 PatSnap. All rights reserved.Legal|Privacy policy|Modern Slavery Act Transparency Statement|Sitemap|About US| Contact US: help@patsnap.com