Hydraulic support welding system and method
A technology of hydraulic support and welding system, applied in welding equipment, welding accessories, arc welding equipment, etc., can solve the problems of poor weld uniformity and consistency, difficult to guarantee production safety, and poor consistency of welded workpieces, and achieve uniformity. Good consistency, saving labor and time, and reducing the effect of location changes
- Summary
- Abstract
- Description
- Claims
- Application Information
AI Technical Summary
Problems solved by technology
Method used
Image
Examples
Embodiment 1
[0039] Such as figure 1 As shown, a hydraulic support welding system includes: 7 welding workstations 1, positioner 2, logistics trolley 3, guide rail, control system, loading rack 5, unloading rack, maintenance platform and safety fence, each welding The workstation 1 includes a welding robot 11, a welding robot 12 and a mobile arm. The welding robot 11 and the welding robot 12 are arc welding robots. The two welding robots are provided with their own independent welding systems. The welding robot 11 and the welding robot 12 are equipped with laser The tracking sensor can track and monitor the weld seam in real time, detect the actual shape of the weld seam, and eliminate the size and shape errors of the weld seam caused by processing, assembly and deformation of the workpiece. The welding robot 11 and the welding robot 12 are located on the moving arm, and the moving arm moves along a direction parallel to the guiding rail, driving two welding robots to move along this direc...
PUM
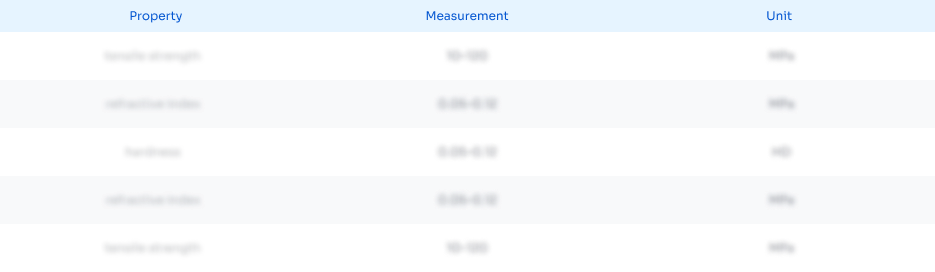
Abstract
Description
Claims
Application Information

- R&D Engineer
- R&D Manager
- IP Professional
- Industry Leading Data Capabilities
- Powerful AI technology
- Patent DNA Extraction
Browse by: Latest US Patents, China's latest patents, Technical Efficacy Thesaurus, Application Domain, Technology Topic, Popular Technical Reports.
© 2024 PatSnap. All rights reserved.Legal|Privacy policy|Modern Slavery Act Transparency Statement|Sitemap|About US| Contact US: help@patsnap.com