Humanoid pneumatic soft robot finger
A pneumatic and pneumatic actuator technology, applied in the direction of manipulators, chucks, manufacturing tools, etc., can solve the problems of inability to balance output force and response time, insufficient output force in response time, poor friendliness and safety, etc., to achieve performance Excellent, impressive output, and fast recovery results
- Summary
- Abstract
- Description
- Claims
- Application Information
AI Technical Summary
Problems solved by technology
Method used
Image
Examples
Embodiment 1
[0045] Such as Figure 1~4 As shown, a humanoid pneumatic soft robot finger in this embodiment has the following structure:
[0046] It includes the front flexible unit 4, the middle flexible phalanx unit 3 and the rear flexible phalanx unit 2; there is a connection between the front flexible unit 4 and the middle flexible phalanx unit 3, and between the middle flexible phalanx unit 3 and the rear flexible phalanx unit 2. Pneumatic actuator unit 1.
[0047] The pneumatic actuator unit has a comb-like structure as a whole, including a base and a plurality of combs arranged side by side along the length of the finger; a main cavity 11 is provided inside the base, and each comb is provided with a The sub-cavities 12 connected to the main cavity;
[0048] Both the middle flexible phalanx unit 3 and the rear flexible phalanx unit 2 are provided with an air passage 5 running through the length direction of the finger, and the air passage 5 passes through the opening 15 arranged on...
PUM
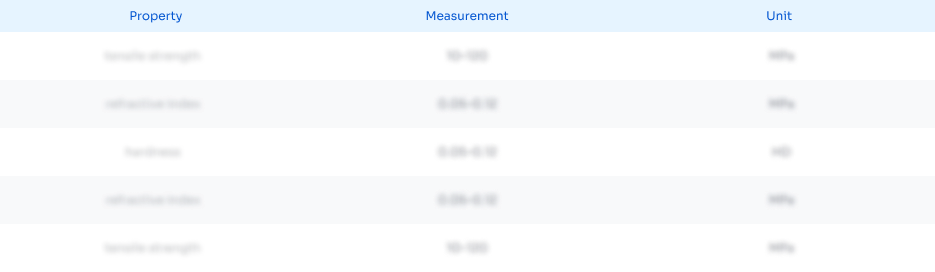
Abstract
Description
Claims
Application Information

- R&D Engineer
- R&D Manager
- IP Professional
- Industry Leading Data Capabilities
- Powerful AI technology
- Patent DNA Extraction
Browse by: Latest US Patents, China's latest patents, Technical Efficacy Thesaurus, Application Domain, Technology Topic, Popular Technical Reports.
© 2024 PatSnap. All rights reserved.Legal|Privacy policy|Modern Slavery Act Transparency Statement|Sitemap|About US| Contact US: help@patsnap.com