Error parameter calibration method for nine-axis sensor
A nine-axis sensor and error parameter technology, applied in the direction of the instrument, can solve the problems of sensor error, equipment positioning, attitude determination performance, low efficiency, etc., and achieve the effect of good universality and good calibration accuracy
- Summary
- Abstract
- Description
- Claims
- Application Information
AI Technical Summary
Problems solved by technology
Method used
Image
Examples
Embodiment Construction
[0076] The technical solutions of the present invention will be further described below in conjunction with the accompanying drawings and embodiments.
[0077] Step 1, such as figure 1 As shown, take the center of the sensor (that is, the mobile phone) as the center of rotation, and make it rotate 720° around the X, Y, and Z axes of the carrier coordinate system;
[0078] Step 2, establish the measurement error model of gyroscope, accelerometer, magnetometer in the nine-axis sensor to determine the calibration parameters, to facilitate the construction of error state Kalman filter for sensor calibration (the present invention considers that the carrier coordinate system is the same as the inertial sensor coordinate system axis system ). Using the Kalman filter to complete the sensor calibration process as figure 2 shown.
[0079] Moreover, the implementation of step 2 includes the following sub-steps,
[0080] 21) Model the original observation model of the gyroscope. Af...
PUM
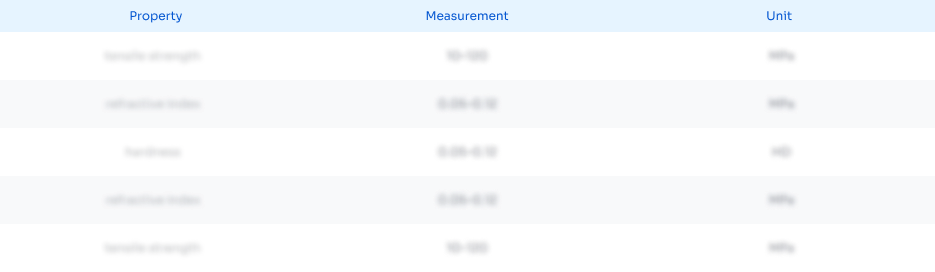
Abstract
Description
Claims
Application Information

- R&D
- Intellectual Property
- Life Sciences
- Materials
- Tech Scout
- Unparalleled Data Quality
- Higher Quality Content
- 60% Fewer Hallucinations
Browse by: Latest US Patents, China's latest patents, Technical Efficacy Thesaurus, Application Domain, Technology Topic, Popular Technical Reports.
© 2025 PatSnap. All rights reserved.Legal|Privacy policy|Modern Slavery Act Transparency Statement|Sitemap|About US| Contact US: help@patsnap.com