Space mechanical arm suspension microgravity simulation method
A space manipulator, microgravity simulation technology, applied in the field of simulation experiments, can solve problems such as the influence of spacecraft attitude, the degree of freedom of the manipulator, the range limit, the moment deviation at the joints, etc.
- Summary
- Abstract
- Description
- Claims
- Application Information
AI Technical Summary
Problems solved by technology
Method used
Image
Examples
specific Embodiment
[0130] Specific embodiments: the space manipulator that needs to unload gravity is simplified as Figure 8 The joint and arm structure with uniform mass shown in the figure, given that the weight of the root joint, elbow joint, and wrist deflection joint is 6kg, the weight of the forearm end deflection joint and end execution joint is 3kg, and the weight of the upper arm and forearm is 10kg . The distance between the root and the elbow is 1060mm, the distance between the elbow and the wrist deflection joint is 1060mm, and the distance between the wrist and the end execution joint is 180mm. The lifting point force at the root of the boom is F1, which is located at a distance of 100mm from the root joint; the force at the hanging point at the elbow is F2; the force at the end of the forearm is F3, which is located at a distance of 725mm from the elbow joint; the force at the hanging point at the wrist is F4; The lifting point force of the terminal execution joint is F5. The ...
PUM
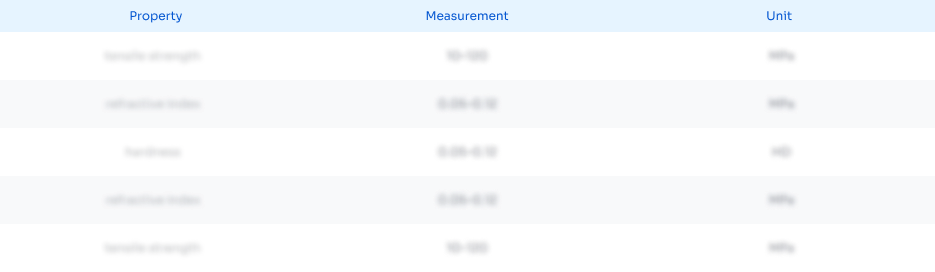
Abstract
Description
Claims
Application Information

- Generate Ideas
- Intellectual Property
- Life Sciences
- Materials
- Tech Scout
- Unparalleled Data Quality
- Higher Quality Content
- 60% Fewer Hallucinations
Browse by: Latest US Patents, China's latest patents, Technical Efficacy Thesaurus, Application Domain, Technology Topic, Popular Technical Reports.
© 2025 PatSnap. All rights reserved.Legal|Privacy policy|Modern Slavery Act Transparency Statement|Sitemap|About US| Contact US: help@patsnap.com