Injection mould for front wall plate of motorcycle
A technology for injection molds and front panels, which is applied to household appliances, other household appliances, household components, etc., can solve the problems of insufficient filling, burning glue, unable to melt plastic filling speed adjustment, etc., achieve rapid cooling and hardening, and reduce waste. Effect
- Summary
- Abstract
- Description
- Claims
- Application Information
AI Technical Summary
Problems solved by technology
Method used
Image
Examples
Embodiment Construction
[0031] The specific implementation manners of the present invention will be further described below in conjunction with the accompanying drawings, so as to make the technical solution of the present invention easier to understand and grasp.
[0032] A motorcycle cowl injection mold, such as figure 1 , figure 2 As shown, a mold body 1 is included, and the mold body 1 includes a fixed mold and a movable mold. After the fixed mold and the movable mold are interlocked, a mold cavity 2 for molding a motorcycle dash panel is formed between the fixed mold and the movable mold.
[0033] Such as figure 2 , image 3 As shown, the mold body 1 is provided with a vent hole 3, one end of the vent hole 3 communicates with the mold cavity 2, and the other end passes through the outer wall of the mold body 1 and communicates with the outside world. When using an injection molding machine to inject molten plastic into the mold cavity 2 , the air in the mold cavity 2 can be exhausted throug...
PUM
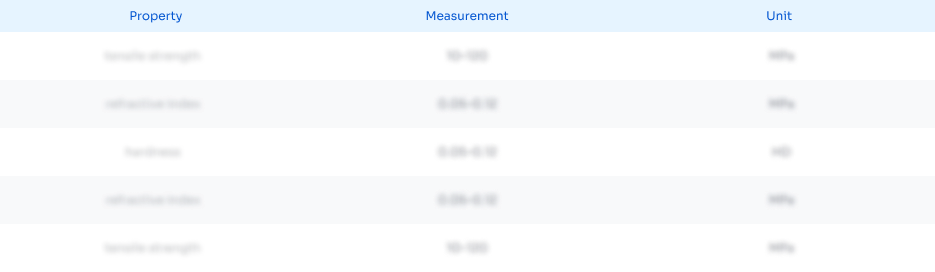
Abstract
Description
Claims
Application Information

- Generate Ideas
- Intellectual Property
- Life Sciences
- Materials
- Tech Scout
- Unparalleled Data Quality
- Higher Quality Content
- 60% Fewer Hallucinations
Browse by: Latest US Patents, China's latest patents, Technical Efficacy Thesaurus, Application Domain, Technology Topic, Popular Technical Reports.
© 2025 PatSnap. All rights reserved.Legal|Privacy policy|Modern Slavery Act Transparency Statement|Sitemap|About US| Contact US: help@patsnap.com