Workpiece machining deformation control method
A control method and processing deformation technology, applied in metal processing, automatic control devices, metal processing equipment, etc., can solve the problems of large deformation of the workpiece, high thermal aging energy consumption, and poor control.
- Summary
- Abstract
- Description
- Claims
- Application Information
AI Technical Summary
Problems solved by technology
Method used
Image
Examples
Embodiment Construction
[0031] In order to enable those skilled in the art to better understand the solutions of the present application, the technical solutions in the embodiments of the present application will be clearly and completely described below in conjunction with the drawings in the embodiments of the present application.
[0032] see figure 1 , which is a flow chart of a method for controlling workpiece machining deformation provided in this embodiment. A method for controlling workpiece machining deformation, comprising the following steps:
[0033] S1: Establish a geometric model of the workpiece to be processed, wherein the geometric model is a two-dimensional geometric model or a three-dimensional geometric model, and the geometric model is composed of the workpiece body and the area to be cut, and the topological sum of the workpiece body and the area to be cut For the workpiece blank.
[0034] S2: Import the geometric model of the workpiece to be processed into the Optistrcut modu...
PUM
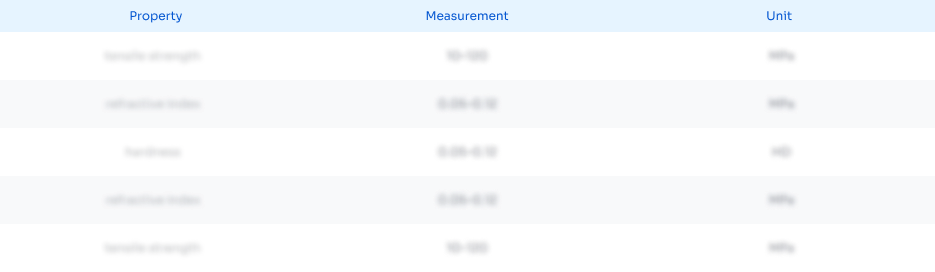
Abstract
Description
Claims
Application Information

- Generate Ideas
- Intellectual Property
- Life Sciences
- Materials
- Tech Scout
- Unparalleled Data Quality
- Higher Quality Content
- 60% Fewer Hallucinations
Browse by: Latest US Patents, China's latest patents, Technical Efficacy Thesaurus, Application Domain, Technology Topic, Popular Technical Reports.
© 2025 PatSnap. All rights reserved.Legal|Privacy policy|Modern Slavery Act Transparency Statement|Sitemap|About US| Contact US: help@patsnap.com