Method for designing low-working-condition rotatable guide vane corner rule of axial flow compressor of ship gas turbine
A technology for axial flow compressors and gas turbines, which is applied in computer-aided design, mechanical equipment, machines/engines, etc., and can solve the surge in the number of samples of angle combination schemes, the difficulty of designing the law of joint regulation of the rotation angle of multiple rows of steerable guide vanes, etc. problems, to simplify the workload of designers, improve surge margin indicators, and reduce resource and time consumption.
- Summary
- Abstract
- Description
- Claims
- Application Information
AI Technical Summary
Problems solved by technology
Method used
Image
Examples
Embodiment Construction
[0032] The present invention will be described in more detail below with reference to the accompanying drawings:
[0033] Combine Figure 1-2 , Specific embodiments of a low operating condition guiding leaf angle regular design method of a ship gas turbine shaft flow gas machine according to the present invention implementation:
[0034] (1) Select the feature section calculated by the transduction leaf angle;
[0035] (2) Extracting the compressor under the design point (all convertible leaf angles at this time), each of the columns of the transduction leaf adjacent rear rushed blade feature cross-sectional position, including: imported axial speed C 1a , Circumferential speed u, import absolute airflow angle α 1 And imported relative airflow angle β 1 ;
[0036] (3) According to the requirements of the transduction leaf rotation angle, the rotational speed N 'and the compressor design point are allocated with the compressor design point, and the moving leaf circumferential veloci...
PUM
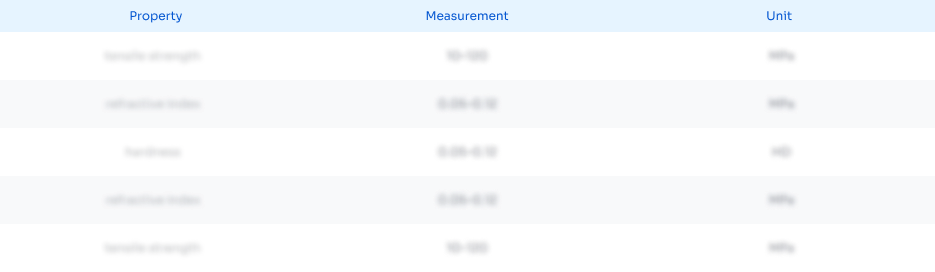
Abstract
Description
Claims
Application Information

- R&D Engineer
- R&D Manager
- IP Professional
- Industry Leading Data Capabilities
- Powerful AI technology
- Patent DNA Extraction
Browse by: Latest US Patents, China's latest patents, Technical Efficacy Thesaurus, Application Domain, Technology Topic, Popular Technical Reports.
© 2024 PatSnap. All rights reserved.Legal|Privacy policy|Modern Slavery Act Transparency Statement|Sitemap|About US| Contact US: help@patsnap.com