Visual servo control method and system using grey prediction model
A gray prediction model and visual servo technology, applied in the field of communication, can solve the problem of untimely control and achieve the effect of precise flight control
- Summary
- Abstract
- Description
- Claims
- Application Information
AI Technical Summary
Problems solved by technology
Method used
Image
Examples
Embodiment 1
[0053] see figure 1 , figure 1 It is a schematic flowchart of a visual servoing control method using a gray prediction model provided by an embodiment of the present invention.
[0054] Such as figure 1 As shown, the first embodiment of the present invention provides a visual servoing control method using a gray prediction model, including the following steps S1 to S4.
[0055] S1. Obtain the actual position of the target collected by the airborne image acquisition device of the drone and the expected position corresponding to the actual position of the target;
[0056] S2. Calculate an output deviation value according to the target actual position and the expected position;
[0057] S3. Obtain the predicted value of the next state of the drone through the gray prediction module;
[0058] S4. Comparing the output deviation value with the prediction value to obtain a prediction error, and controlling the UAV according to the prediction error.
[0059] Here, the onboard ima...
Embodiment 2
[0061] It also includes control parameters to control the attitude, angle and speed of the UAV flight. After calculating the output deviation value according to the actual position of the target and the expected position, visual servo control is also included, and the visual servo control includes:
[0062] Obtaining the image feature error between the actual position of the target and the expected position of the drone flying, and establishing a servo relationship between the image feature error and the speed;
[0063] The position controller is used to calculate the speed control law according to the servo relationship, and the desired attitude is obtained through the speed control law;
[0064] The attitude tracking control of UAV is carried out by sliding mode control.
[0065] Specifically, see figure 2 and image 3 , figure 2 It is a flow chart of image-based visual servoing control according to the second embodiment of the present invention. image 3 It is a visu...
Embodiment 3
[0067] The gray prediction module includes a GM(1,1) model, and the GM(1,1) model performs position accuracy prediction through an adjustment factor.
[0068] Specifically, see Figure 4 , Figure 4 It is the basic frame diagram of the gray prediction module of the third embodiment of the present invention. Propose an improved gray prediction model based on the background value of the adjustment factor. The traditional GM (1,1) model is more widely used in the gray prediction theory. The present invention proposes a new background value with an adjustment factor and changes the initial condition. Combined with the new GM(1,1) model, the optimization method of the adjustment factor is proposed, and it is applied to the modeling of the visual servo control system of the flying robot. The new model has passed the simulation and prediction comparison of the pure exponential sequence. It can be seen that the new model of GM(1,1) optimized by the adjustment factor has higher accur...
PUM
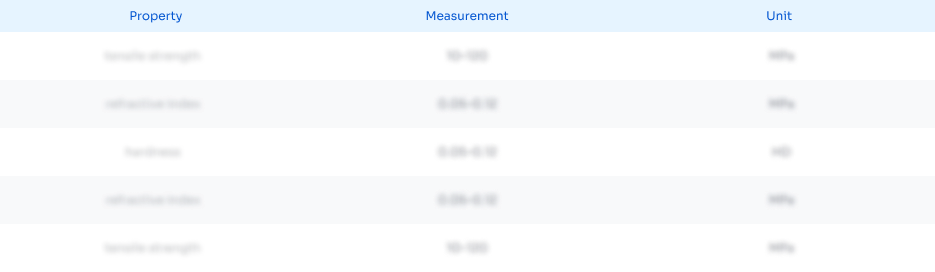
Abstract
Description
Claims
Application Information

- R&D
- Intellectual Property
- Life Sciences
- Materials
- Tech Scout
- Unparalleled Data Quality
- Higher Quality Content
- 60% Fewer Hallucinations
Browse by: Latest US Patents, China's latest patents, Technical Efficacy Thesaurus, Application Domain, Technology Topic, Popular Technical Reports.
© 2025 PatSnap. All rights reserved.Legal|Privacy policy|Modern Slavery Act Transparency Statement|Sitemap|About US| Contact US: help@patsnap.com