Foamed wood composite board production and manufacturing process
A manufacturing process and technology of composite panels, which are applied in the direction of flat products, household appliances, other household appliances, etc., can solve the problems of flame retardant, low sound insulation and thermal insulation performance, the board cannot be quickly ejected, and the foam material cannot be injected. Achieve the effect of good processing effect, light weight and easy collection
- Summary
- Abstract
- Description
- Claims
- Application Information
AI Technical Summary
Problems solved by technology
Method used
Image
Examples
Embodiment Construction
[0033] The embodiments of the present invention will be described in detail below with reference to the accompanying drawings, but the present invention can be implemented in many different ways defined and covered by the claims.
[0034] Such as Figure 1 to Figure 5 As shown, a foamed wood composite board production and manufacturing process, the foamed wood composite board production and manufacturing process adopts the following processing equipment, the processing equipment includes a base plate 1, a fixed formwork 2 and a movable formwork 3, the base plate 1 The middle part of the upper end is equipped with a fixed formwork 2, and a movable formwork 3 is arranged above the fixed formwork 2, and the lower end of the movable formwork 3 is installed on the base plate 1.
[0035] The fixed formwork 2 includes a fixed frame 21, a jacking frame 22, a cleaning unit 23, a telescopic rod 24 and a telescopic spring 25. The upper end of the base plate 1 is equipped with a fixed fra...
PUM
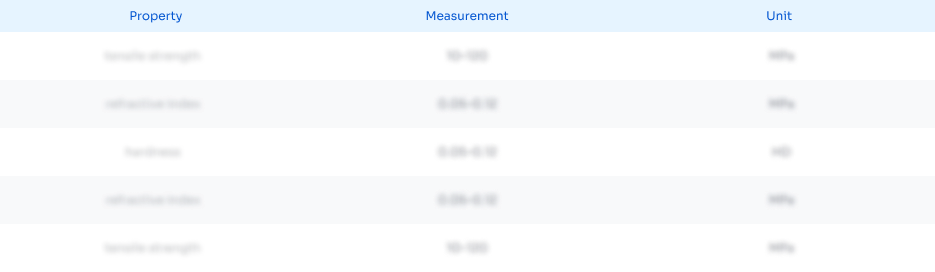
Abstract
Description
Claims
Application Information

- Generate Ideas
- Intellectual Property
- Life Sciences
- Materials
- Tech Scout
- Unparalleled Data Quality
- Higher Quality Content
- 60% Fewer Hallucinations
Browse by: Latest US Patents, China's latest patents, Technical Efficacy Thesaurus, Application Domain, Technology Topic, Popular Technical Reports.
© 2025 PatSnap. All rights reserved.Legal|Privacy policy|Modern Slavery Act Transparency Statement|Sitemap|About US| Contact US: help@patsnap.com