Integrated mold structure and method used for optical fiber
An integrated, mold technology, applied in the field of optical cable production, can solve the problems of difficult adjustment of the sheath, time-consuming, high cost, and achieve the effect of facilitating threading and guiding, reducing production costs, and ensuring the molding effect.
- Summary
- Abstract
- Description
- Claims
- Application Information
AI Technical Summary
Problems solved by technology
Method used
Image
Examples
Embodiment Construction
[0022] The present invention will be further described below in conjunction with the accompanying drawings and specific embodiments, so that those skilled in the art can better understand the present invention and implement it, but the examples given are not intended to limit the present invention.
[0023] refer to Figure 1-4 As shown, an integrated mold structure for optical cables includes a double-layer co-extrusion mechanism and a straightening mechanism. It includes a mold core body and a mold sleeve. At least one fiber channel and at least one reinforcement channel are arranged in the axial direction of the mold core body. The fiber inlet and the fiber inlet corresponding to the fiber channel and the reinforcement channel are arranged on the mold sleeve. Reinforcing member inlet; the front end of the mold core body is tapered, and the front end of the mold core body cooperates with the tapered hole of the mold sleeve to form a tapered flow channel, and the mold sleeve ...
PUM
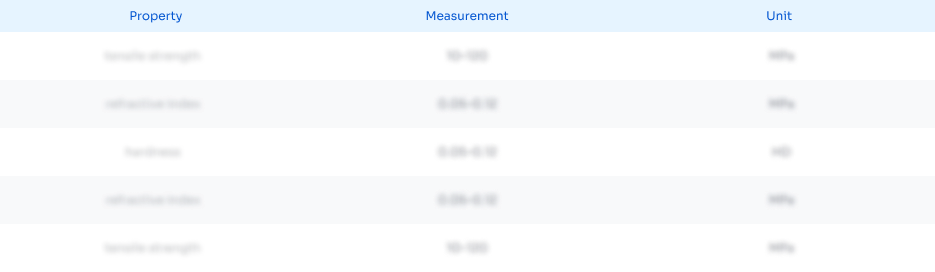
Abstract
Description
Claims
Application Information

- R&D Engineer
- R&D Manager
- IP Professional
- Industry Leading Data Capabilities
- Powerful AI technology
- Patent DNA Extraction
Browse by: Latest US Patents, China's latest patents, Technical Efficacy Thesaurus, Application Domain, Technology Topic, Popular Technical Reports.
© 2024 PatSnap. All rights reserved.Legal|Privacy policy|Modern Slavery Act Transparency Statement|Sitemap|About US| Contact US: help@patsnap.com