Robot joint module
A technology of robot joints and modules, which is applied in the field of robots, can solve the problems of chaotic wiring, heavy weight, and difficult maintenance of parts, and achieve the effect of convenient follow-up maintenance, simple and compact structure, and preventing chaotic wiring
- Summary
- Abstract
- Description
- Claims
- Application Information
AI Technical Summary
Problems solved by technology
Method used
Image
Examples
Embodiment Construction
[0022] Now in conjunction with the accompanying drawings, the preferred embodiments of the present invention will be described in detail.
[0023] like Figure 1-5 As shown, the present invention provides a robot joint module, which includes a module end cover 1, a circuit board 2, an encoder code disc, a motor, a brake 6, a reducer 8 and a reducer output shaft 9, wherein the The encoder code disc includes the first code disc 3 of the encoder for measuring the rotation angle of the output shaft 9 of the reducer, and the second code disc 4 of the encoder for measuring the rotation angle of the motor, and the motor driver circuit is arranged on the circuit board 2 , motor input end read head circuit and reducer output end read head circuit, motor input end read head circuit, reducer output end read head circuit corresponding to encoder second code disc 4, encoder first code disc 3 position setting respectively. The first code disc 3 of the encoder is set to measure the rotation...
PUM
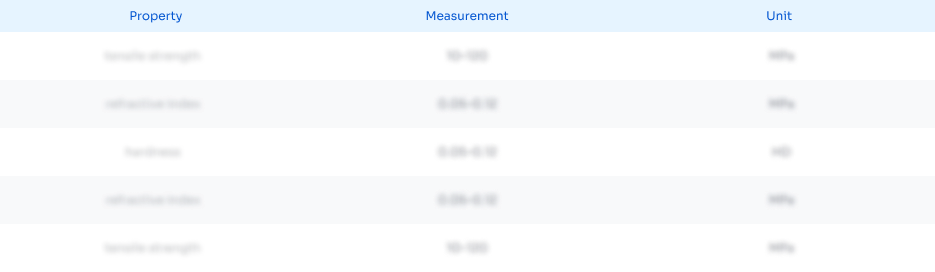
Abstract
Description
Claims
Application Information

- R&D Engineer
- R&D Manager
- IP Professional
- Industry Leading Data Capabilities
- Powerful AI technology
- Patent DNA Extraction
Browse by: Latest US Patents, China's latest patents, Technical Efficacy Thesaurus, Application Domain, Technology Topic, Popular Technical Reports.
© 2024 PatSnap. All rights reserved.Legal|Privacy policy|Modern Slavery Act Transparency Statement|Sitemap|About US| Contact US: help@patsnap.com