Manufacturing method of embedded cavity and PCB
A manufacturing method and a technology for burying a cavity, which are applied in the manufacture of printed circuits, printed circuits and electrical components connected with non-printed electrical components, etc. The effect of large transmission and shielding area
- Summary
- Abstract
- Description
- Claims
- Application Information
AI Technical Summary
Problems solved by technology
Method used
Image
Examples
Embodiment 1
[0048] see Figure 1-Figure 7 , the present embodiment provides a method for manufacturing an embedded cavity, comprising the steps of:
[0049] Step 100 , setting the cavity area of the signal line core board 30 .
[0050] In this step, the signal line core board 30 is a copper clad laminate with a predetermined signal line pattern 31 fabricated on one board surface. It should be known that the size and shape of the cavity 40 can be adjusted adaptively according to different requirements or application scenarios. In this step, setting the cavity area is used to define the desired shape and size of the cavity.
[0051] For details, please refer to Figure 6 , the cavity area is Figure 6 In the surface area of the signal line core board 30 within the dotted line frame, it should be noted that, in practical applications, the predetermined signal line pattern 31 may be entirely located in the cavity area, or may be partially located in the cavity area.
[0052] Step 110 ...
Embodiment approach
[0064] As another specific implementation manner, this step specifically includes:
[0065] Aligning the step groove 11 and the avoidance channel 21, making the step groove 11 pass through the avoidance channel 21, and stacking the prepreg 20 on the optical core board 10;
[0066] The cavity area and the stepped groove 11 are aligned, and the signal line core board 10 is stacked on the prepreg 20 so that the cavity area is covered in the notch of the stepped groove 11 .
[0067] Step 140 , pressing to form a multi-layer board with the cavity 40 embedded therein.
[0068] The above-mentioned laminated signal line core board 30, prepreg 20, and metallized optical core board 10 are hot-pressed, and related board edge processing procedures are performed to form a multi-layer board; inside the multi-layer board, the stepped groove 11 It is in contact with the board surface of the signal line core board 30 and surrounds a cavity 40 forming a metallized cavity wall with the board su...
Embodiment 2
[0082] This embodiment also provides a PCB, in which a closed cavity 40 is embedded, and the cavity 40 is manufactured according to the manufacturing method provided in the first embodiment.
[0083] In the PCB of this embodiment, the stepped groove 11 is processed by a thick base material core board and matched with the corresponding groove on the prepreg 20, and the alignment method of the line and the cavity 40 is optimized by the alignment between the prepreg 20 and the signal line core board 30 Because the thick core board and the signal line core board 30 are directly aligned, the alignment is better, the shape of the cavity 40 is good, and the manufacturing method is simple.
PUM
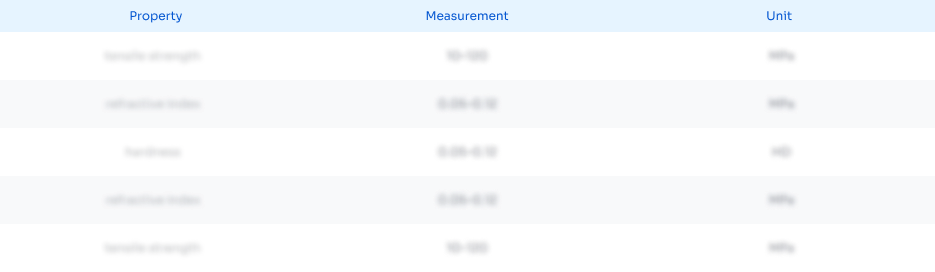
Abstract
Description
Claims
Application Information

- R&D Engineer
- R&D Manager
- IP Professional
- Industry Leading Data Capabilities
- Powerful AI technology
- Patent DNA Extraction
Browse by: Latest US Patents, China's latest patents, Technical Efficacy Thesaurus, Application Domain, Technology Topic, Popular Technical Reports.
© 2024 PatSnap. All rights reserved.Legal|Privacy policy|Modern Slavery Act Transparency Statement|Sitemap|About US| Contact US: help@patsnap.com