A method and device for infrared temperature drift correction based on Kalman filter
A Kalman filter and temperature drift correction technology, applied in the field of infrared temperature measurement, can solve problems such as affecting temperature measurement efficiency, and achieve the effect of improving temperature measurement efficiency and eliminating temperature jitter
- Summary
- Abstract
- Description
- Claims
- Application Information
AI Technical Summary
Problems solved by technology
Method used
Image
Examples
Embodiment 1
[0049] Such as figure 1 , the invention discloses a Kalman filter-based infrared temperature drift correction method, comprising:
[0050] S100. Convert the collected target thermal radiation signal into a corresponding electrical signal, and obtain a corresponding digital real-time response value through voltage amplification and AD conversion of the electrical signal;
[0051] Specifically, the step S100 includes: selecting the center point of the infrared image as the calibration point, obtaining the DC digitized component x16 value of the target radiation from the center point of the infrared image, and denoting it as g1; The digitized component x16 value at the point is recorded as g0, and the digitized real-time response s is obtained according to the difference between g1 and g0.
[0052] S200. Calculate the compensated response value according to the increment between the two shutters and the increment of the lens barrel temperature; specifically, S200 specifically incl...
Embodiment 2
[0082] The embodiment of the present invention discloses an infrared temperature drift correction device based on a Kalman filter, such as Figure 4 , including a data acquisition unit 1, an iterative temperature drift compensation unit 2, a temperature calculation unit 3, and a Kalman temperature drift correction unit 4;
[0083] The data acquisition unit 1 collects the target thermal radiation signal and converts it into a corresponding electrical signal, and the electrical signal is amplified by voltage and converted by AD to obtain a corresponding digital real-time response value;
[0084] Specifically, the center point of the infrared image is selected as the calibration point, and the x16 value of the DC digitized component of the target radiation is obtained from the center point of the infrared image, which is recorded as g1; The x16 value of the component is recorded as g0, and the digital real-time response value s is obtained according to the difference between g1 a...
PUM
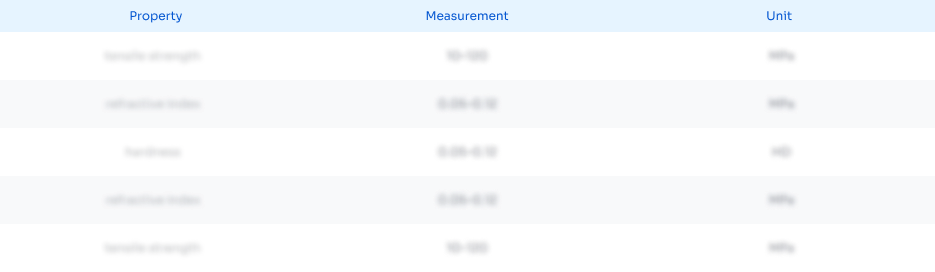
Abstract
Description
Claims
Application Information

- Generate Ideas
- Intellectual Property
- Life Sciences
- Materials
- Tech Scout
- Unparalleled Data Quality
- Higher Quality Content
- 60% Fewer Hallucinations
Browse by: Latest US Patents, China's latest patents, Technical Efficacy Thesaurus, Application Domain, Technology Topic, Popular Technical Reports.
© 2025 PatSnap. All rights reserved.Legal|Privacy policy|Modern Slavery Act Transparency Statement|Sitemap|About US| Contact US: help@patsnap.com