Welding robot moving mechanism
A welding robot and mobile mechanism technology, applied in welding equipment, auxiliary welding equipment, welding/cutting auxiliary equipment, etc., can solve the problems of unfavorable flange and web welding, troublesome movement of welding robots, inconvenient handling of equipment, etc., and achieve improvement Structural strength and overall firmness, ensuring coherence and stability, and improving the effect of moving stability and safety
- Summary
- Abstract
- Description
- Claims
- Application Information
AI Technical Summary
Problems solved by technology
Method used
Image
Examples
Embodiment
[0034] Example: such as Figure 1-5 As shown, a welding robot moving mechanism includes a support frame 9, a beam 90 is fixed on the support frame 9, and a sliding mechanism 900 is arranged along the length direction of the beam 90; a robot support seat 910 slidably assembled on the sliding mechanism 900, The welding robot 920 is assembled on the robot supporting base 910, and the welding machine moving mechanism 930 is arranged on the robot supporting base 910. The welding machine moving mechanism 930 can drive the welding robot 910 to translate along the sliding mechanism 900; The welding machine moving mechanism is set, and the welding robot translates along the sliding mechanism; the moving stability and safety of the welding robot are improved, and the welding robot is very convenient to move.
[0035] The robot support base 910 has an "L"-shaped structure, including a transverse plate 911 and a longitudinal plate 912; the transverse plate 911 and the longitudinal plate 9...
PUM
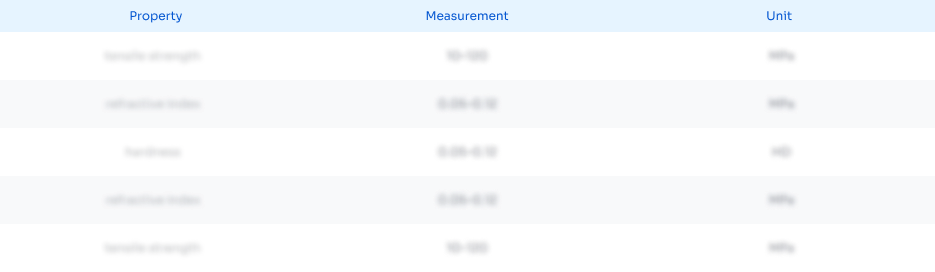
Abstract
Description
Claims
Application Information

- Generate Ideas
- Intellectual Property
- Life Sciences
- Materials
- Tech Scout
- Unparalleled Data Quality
- Higher Quality Content
- 60% Fewer Hallucinations
Browse by: Latest US Patents, China's latest patents, Technical Efficacy Thesaurus, Application Domain, Technology Topic, Popular Technical Reports.
© 2025 PatSnap. All rights reserved.Legal|Privacy policy|Modern Slavery Act Transparency Statement|Sitemap|About US| Contact US: help@patsnap.com