Method for improving impact toughness of TMCP steel for ships through texture control
A technology for impact toughness and marine use, which is applied in the field of improving the impact toughness of TMCP steel for marine using texture control technology, can solve problems such as affecting the low temperature toughness of steel plates, small anisotropy of mechanical properties, and deteriorating low temperature toughness of steel plates, and achieves the production process. The effect of stability, low implementation difficulty and stable performance
Active Publication Date: 2020-12-25
NORTHEASTERN UNIV +1
View PDF4 Cites 1 Cited by
- Summary
- Abstract
- Description
- Claims
- Application Information
AI Technical Summary
Problems solved by technology
[0005] Texture strengthening is an additional geometric strengthening of controlled-rolled high-strength steel. However, in the production and research of ship plate steel, the influence of texture factors on the low-temperature toughness of steel plates was often ignored.
In fact, the crystallographic orientation can significantly affect the low-temperature to
Method used
the structure of the environmentally friendly knitted fabric provided by the present invention; figure 2 Flow chart of the yarn wrapping machine for environmentally friendly knitted fabrics and storage devices; image 3 Is the parameter map of the yarn covering machine
View moreImage
Smart Image Click on the blue labels to locate them in the text.
Smart ImageViewing Examples
Examples
Experimental program
Comparison scheme
Effect test
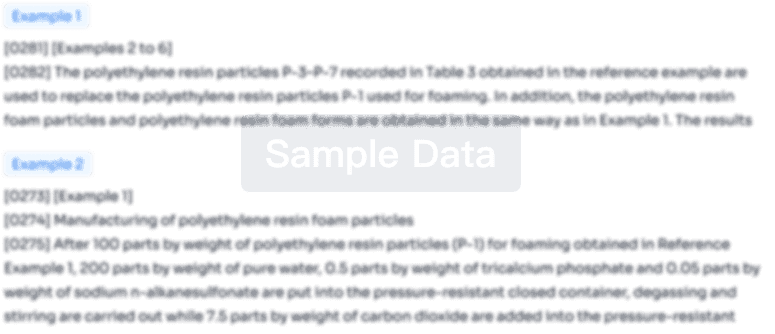
PUM
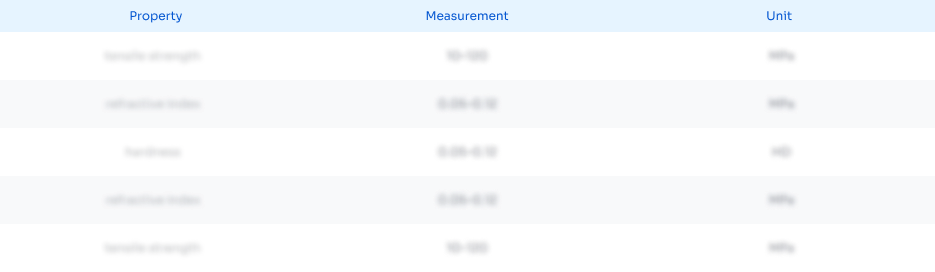
Abstract
The invention discloses a method for improving the impact toughness of TMCP steel for ships through texture control. According to the method, conventional industrial EH47 continuous casting billets are used as raw materials, a TMCP two-stage controlled rolling process is adopted, intermediate billet deformation distribution is controlled under the conditions of a low compression ratio and a high finishing rolling temperature, and the four-stage cooling method of air cooling, water cooling, air cooling and water cooling is adopted after rolling so that high-strength texture distribution is obtained at the center of a steel plate; and the impact energy of the steel plate under the condition of -80 DEG C is improved by adopting a high-strength favorable texture of the core part of the steel plate and a uniformly distributed high-content {110} slip surface. According to the production method, the impact toughness of the steel plate at the temperature of -80 DEG C can be obviously improved,the production process is simple, the operability is high, the implementation difficulty is low, and the texture control effect is obvious.
Description
technical field [0001] The invention belongs to the field of steel plate manufacturing for ships, and in particular relates to a method for improving the impact toughness of TMCP steel for ships by utilizing texture control technology. Background technique [0002] In recent years, with the large-scale development of ships, the safety of ships has been seriously challenged, which has led to the rapid development of large-thickness ship steel with excellent low-temperature toughness. When the TMCP process is used to produce steel for ships, low-carbon microalloying treatment and a certain amount of Ni element are added in terms of composition, and the total compression ratio in the rolling process is increased and the deformation in the rough rolling stage and the deformation in the finishing rolling stage are optimized. amount, and finally change the flattened state of the austenite after final rolling, coupled with a suitable post-rolling cooling procedure, to achieve the r...
Claims
the structure of the environmentally friendly knitted fabric provided by the present invention; figure 2 Flow chart of the yarn wrapping machine for environmentally friendly knitted fabrics and storage devices; image 3 Is the parameter map of the yarn covering machine
Login to View More Application Information
Patent Timeline

IPC IPC(8): C21D8/02B21B37/74
CPCB21B37/74C21D8/0205C21D8/0226C21D2211/002C21D2211/005
Inventor 田勇王红涛叶其斌王昭东王国栋赵晋斌邱保文
Owner NORTHEASTERN UNIV
Features
- R&D
- Intellectual Property
- Life Sciences
- Materials
- Tech Scout
Why Patsnap Eureka
- Unparalleled Data Quality
- Higher Quality Content
- 60% Fewer Hallucinations
Social media
Patsnap Eureka Blog
Learn More Browse by: Latest US Patents, China's latest patents, Technical Efficacy Thesaurus, Application Domain, Technology Topic, Popular Technical Reports.
© 2025 PatSnap. All rights reserved.Legal|Privacy policy|Modern Slavery Act Transparency Statement|Sitemap|About US| Contact US: help@patsnap.com