High temperature anti-oxidation carbon coating and preparation method
A technology for oxidizing carbon and coatings, which is applied in the field of carbon preparation, and can solve problems such as poor sealing of carbon brick gaps, poor paste performance, and damage to the furnace body, and achieve high oxidation resistance and resistance to acid and alkaline substances Strong corrosion resistance and high mechanical strength
- Summary
- Abstract
- Description
- Claims
- Application Information
AI Technical Summary
Problems solved by technology
Method used
Image
Examples
Embodiment 1
[0020] The raw materials are composed by weight: 34% electro-calcined anthracite powder, 15% silicon carbide fine powder, 8% graphite powder, 8% andalusite fine powder, 35% binder, electro-calcined anthracite powder The resistivity is 440Ω, the fineness is not less than 200 mesh, the silicon content of silicon carbide fine powder is 98%, the fineness is not less than 200 mesh, the degree of graphitization in the graphite powder is 99%, the fineness is not less than 200 mesh, and the fineness of andalusite is not less than 200 For this purpose, the adhesive is selected from CAROBRES T60 carbon-containing resin.
[0021] First dry-mix the electro-calcined anthracite powder, silicon carbide fine powder, graphite powder and andalusite fine powder, and after mixing evenly, preheat the adhesive to 30°C, then disperse the above mixed powder into the adhesive and stir. 5 hours until the mixture is uniform to obtain a coating.
Embodiment 2
[0023] The raw materials are composed by weight: 25% electric calcined anthracite powder, 12% silicon carbide fine powder, 5% graphite powder, 5% andalusite fine powder, 20% binder, calcined anthracite powder The resistivity is 400Ω, the fineness is not less than 200 mesh, the silicon content of the silicon carbide fine powder is 98%, the fineness is not less than 200 mesh, the degree of graphitization in the graphite powder is 99%, the fineness is not less than 200 mesh, and the fineness of andalusite is not less than 200 For this purpose, the adhesive is selected from carbon-containing resin CAROBRES T60.
[0024] First dry-mix the electro-calcined anthracite powder, silicon carbide fine powder, graphite powder, and andalusite fine powder, and after mixing evenly, preheat the adhesive to 40°C, then disperse the above mixed powder into the adhesive and stir. 5.5 hours until the mixture is uniform to obtain a coating.
Embodiment 3
[0026] The raw materials are composed by weight: 30% electric calcined anthracite powder, 20% silicon carbide fine powder, 10% graphite powder, 10% andalusite fine powder, 38% binder, calcined anthracite powder The resistivity is 420Ω, the fineness is not less than 200 mesh, the silicon content of the silicon carbide fine powder is 98%, the fineness is not less than 200 mesh, the degree of graphitization in the graphite powder is 99%, the fineness is not less than 200 mesh, and the fineness of andalusite is not less than 200 For this purpose, the adhesive is selected from carbon-containing resin CAROBRES T60.
[0027] First dry-mix electro-calcined anthracite powder, silicon carbide fine powder, graphite powder, and andalusite fine powder, and after mixing evenly, preheat the adhesive to 50°C, then disperse the above mixed powder into the adhesive and stir. 6 hours until the mixture is uniform to obtain a coating.
[0028] (1), after the paint samples prepared by these three ...
PUM
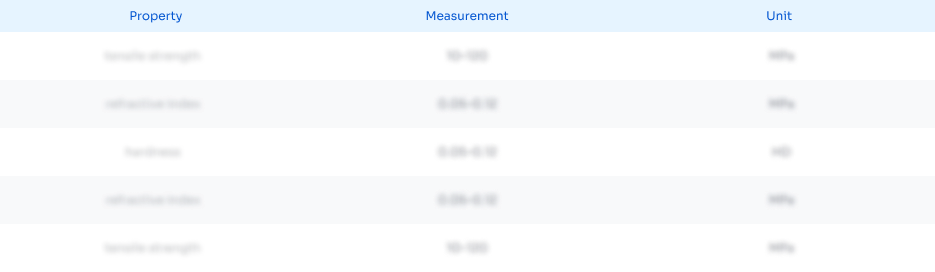
Abstract
Description
Claims
Application Information

- R&D
- Intellectual Property
- Life Sciences
- Materials
- Tech Scout
- Unparalleled Data Quality
- Higher Quality Content
- 60% Fewer Hallucinations
Browse by: Latest US Patents, China's latest patents, Technical Efficacy Thesaurus, Application Domain, Technology Topic, Popular Technical Reports.
© 2025 PatSnap. All rights reserved.Legal|Privacy policy|Modern Slavery Act Transparency Statement|Sitemap|About US| Contact US: help@patsnap.com