Steel rail dynamic damping composite vibration absorber and manufacturing method thereof
A technology of dynamic damping and vibration absorber, applied in the field of rail transit, to achieve the effect of small additional mass, simple structure, and suppression of resonance
- Summary
- Abstract
- Description
- Claims
- Application Information
AI Technical Summary
Problems solved by technology
Method used
Image
Examples
Embodiment 1
[0041] as attached Figure 1-11 As shown, this embodiment proposes a rail dynamic damping composite vibration absorber, the composite vibration absorber 12 is connected to the rail 10, and the composite vibration absorber 12 is arranged between any two adjacent sleepers 11, the composite vibration absorber 12 The shock absorber 12 includes a shock absorber 3 and a fixing device, the shock absorber 3 is arranged in the fixing device, and an accommodation space 9 is formed between the shock absorber 3 and the fixing device, the rail bottom 2 of the rail 10 and At least part of the rail waist 1 is arranged in the receiving space 9; the vibration damper 3 comprises a dynamic vibration absorber and a particle damper.
[0042] Therefore, by wrapping the rail bottom 2 and at least part of the rail waist 1 of the rail 10 with the composite shock absorber 12, and combining the dynamic shock absorber and the particle damper of the shock absorber 3, both advantages of the two are combine...
Embodiment approach
[0052] Mode 1, the base plate 4 is provided with a groove 8, and the protection member 5 is plugged into the groove 8, which is conducive to further ensuring the reliability of the assembly between the base plate 4, the protection member 5, and the shock absorber 3;
[0053] Among them, as attached Figure 6 , attached Figure 9 For example, at least one groove 8 is provided on the bottom plate 4, and the protective member 5 includes a first plate body 52, a second plate body 53, a third plate body 54, a fourth plate body 55, and the second plate body body 53, the third plate body 54, and the fourth plate body 55 are connected sequentially, and the first plate body 52 is connected with the upper end surfaces of the second plate body 53, the third plate body 54, and the fourth plate body 55 at the same time; The second plate body 53, the third plate body 54, and the fourth plate body 55 are all inserted into the groove 8; the first plate body 52 is attached to the upper surfac...
Embodiment 2
[0061] In Example 1, the composite vibration absorber 12 coordinates the vibration-absorbing effect of the resonant rod 31 through the dynamics, the particle damping and vibration-reducing effect of the damping box 32, and the damping and vibration-reducing effect of the matrix 34, but these types of vibration-damping structures are often In the glass transition temperature region or within a certain range of vibration frequency, the resonance effect or damping effect is the largest. At this time, the internal friction caused by the resonance principle in the composite vibration absorber 12 is the largest, and the vibration reduction effect is the most obvious, so that The composite vibration absorber 12 has certain limitations in actual use.
[0062] Therefore, in order to meet the requirements for rail vibration reduction in some special road sections or key projects, further improve the vibration reduction effect of the composite vibration absorber 12; this embodiment propos...
PUM
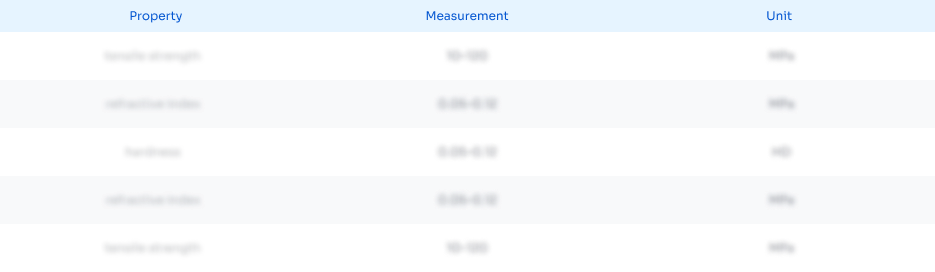
Abstract
Description
Claims
Application Information

- R&D
- Intellectual Property
- Life Sciences
- Materials
- Tech Scout
- Unparalleled Data Quality
- Higher Quality Content
- 60% Fewer Hallucinations
Browse by: Latest US Patents, China's latest patents, Technical Efficacy Thesaurus, Application Domain, Technology Topic, Popular Technical Reports.
© 2025 PatSnap. All rights reserved.Legal|Privacy policy|Modern Slavery Act Transparency Statement|Sitemap|About US| Contact US: help@patsnap.com