Core lamination manufacturing method
A manufacturing method and technology of core laminations, applied in the field of core laminations manufacturing, can solve problems such as difficulty in precise control of the thickness of the adhesive layer, breakage of scattered pieces, easy broken wires, etc., and avoid the design and processing of high-precision lamination tooling, strength and The toughness requirement is low, and the effect of eliminating the vibration noise of the iron core
- Summary
- Abstract
- Description
- Claims
- Application Information
AI Technical Summary
Problems solved by technology
Method used
Image
Examples
Embodiment 1
[0055] The manufacturing method of iron core lamination comprises the following steps:
[0056] The method for manufacturing iron core laminations is characterized in that it comprises the following steps:
[0057] 1. Align and stack the loose cores of the same type into a stack of loose cores;
[0058] 2. Connect and fix the peripheral part of the iron core loose piece stack that exceeds the margin of the finished iron core, without affecting the quality of the finished iron core;
[0059] 3. Use the cutting method to process the inner hole of the iron core;
[0060] Four. If figure 1 As shown, the upper and lower inner pressure plates are respectively placed on the upper and lower ends of the core loose piece stack, and the inner pressure plate fasteners are used to press the upper and lower inner pressure plates on the upper and lower ends of the iron core loose piece stack to fix them with the iron core loose piece stack. The radial dimension of the upper inner pressure...
Embodiment 2
[0074] Based on the manufacturing method of core laminations in implementation 1, in step 4, the top and bottom of the stack of loose cores are coated or stacked with insulating materials, such as silicone grease coating, or stacked release paper, etc., to facilitate later dipping After curing and forming, it will be separated from the tooling.
[0075] Preferably, in step 1, the core loose pieces have no holes or slots passing through from top to bottom.
[0076] Preferably, in step 1, according to the weight of the loose iron core pieces of the model, the required amount of loose iron core pieces is weighed according to the stacking coefficient.
[0077] Preferably, in step 2, the peripheral part of the stack of loose pieces of the iron core that exceeds the margin of the shaped iron core is connected and fixed by means of welding, bonding, riveting or buckling.
[0078] Preferably, in step 3, cutting methods such as wire cutting and laser cutting are used to complete the i...
Embodiment 3
[0084] Based on the manufacturing method of core laminations in implementation 1, in step 6, the viscose surface is immersed in the axis of the lamination stack, and a part of the lamination stack is exposed above the viscose surface.
[0085] Preferably, in step 6, pretreatment (for example, drying, preheating, etc.) before dipping is performed on the stack of scattered iron cores fixed by the inner pressure plate, and then the stack of scattered iron cores fixed by the inner pressure plate is placed horizontally in the container In the viscose.
[0086] Preferably, in step 6, before placing the container into the oven and placing the stack of loose iron cores fixed by the inner pressure plate horizontally in the glue in the container, preheat the vacuum oven, and the preheating temperature is lower than that of the glue curing temperature.
PUM
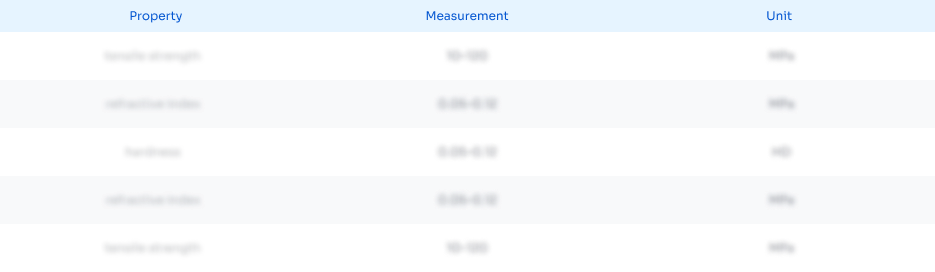
Abstract
Description
Claims
Application Information

- R&D
- Intellectual Property
- Life Sciences
- Materials
- Tech Scout
- Unparalleled Data Quality
- Higher Quality Content
- 60% Fewer Hallucinations
Browse by: Latest US Patents, China's latest patents, Technical Efficacy Thesaurus, Application Domain, Technology Topic, Popular Technical Reports.
© 2025 PatSnap. All rights reserved.Legal|Privacy policy|Modern Slavery Act Transparency Statement|Sitemap|About US| Contact US: help@patsnap.com