Group hole measurement swing angle planning method based on three-coordinate probe
A three-coordinate and stylus technology, applied to measuring devices, instruments, etc., can solve problems such as reducing the efficiency of group holes, and achieve the effects of improving calibration efficiency and reducing swing angles
- Summary
- Abstract
- Description
- Claims
- Application Information
AI Technical Summary
Problems solved by technology
Method used
Image
Examples
Embodiment 1
[0029] A three-coordinate stylus-based pendulum angle planning method for group hole measurement, characterized in that it includes:
[0030] 1) According to the characteristic parameters of the stylus and the hole to be measured, solve the limit angle α at which the stylus does not interfere with the hole;
[0031] 2) Divide the range of the two swing angles of the measuring machine / machine tool evenly at an interval of 2α to generate the machine tool node Ai;
[0032] 3) Solve the pendulum angle of the machine tool in the same direction as the axis of all holes, and use these pendulums as elements to establish a set X ;
[0033] 4) at X In , find the number of elements whose angles with each node do not exceed α;
[0034] 5) Take out the node Aii with the largest number of elements, and the set of holes corresponding to the elements contained in it Yi That is, the set of holes measured using the swing angle of the machine tool corresponding to node Aii;
[0035] 6) if ...
Embodiment 2
[0038] figure 1 A flow chart of a planning method for group hole measurement swing angle based on a three-coordinate stylus provided in an embodiment of the present invention, specifically including the following steps:
[0039] 1) According to the characteristic parameters of the stylus and the hole to be measured, solve the limit angle α at which the stylus does not interfere with the hole;
[0040] 2) Divide the range of the two swing angles of the measuring machine / machine tool evenly at an interval of 2α to generate the machine tool node Ai;
[0041] 3) Solve the pendulum angle of the machine tool in the same direction as the axis of all holes, and use these pendulums as elements to establish a set X ;
[0042] 4) at X In , find the number of elements whose angles with each node do not exceed α;
[0043] 5) Take out the node Aii with the largest number of elements, and the set of holes corresponding to the elements contained in it Yi That is, the set of holes measur...
PUM
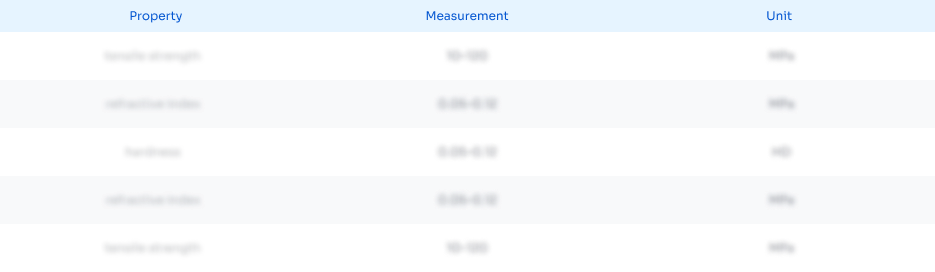
Abstract
Description
Claims
Application Information

- Generate Ideas
- Intellectual Property
- Life Sciences
- Materials
- Tech Scout
- Unparalleled Data Quality
- Higher Quality Content
- 60% Fewer Hallucinations
Browse by: Latest US Patents, China's latest patents, Technical Efficacy Thesaurus, Application Domain, Technology Topic, Popular Technical Reports.
© 2025 PatSnap. All rights reserved.Legal|Privacy policy|Modern Slavery Act Transparency Statement|Sitemap|About US| Contact US: help@patsnap.com