Drilling traction robot support mechanism test device
A supporting mechanism and testing device technology, which is applied in machine gear/transmission mechanism testing, machine/structural component testing, measuring devices, etc., can solve problems such as complex structure of experimental devices, reference of experimental data, and long experimental preparation period, etc., to achieve The effects of reduced experiment preparation period, reduced experiment cost, and simple structure of the experimental device
- Summary
- Abstract
- Description
- Claims
- Application Information
AI Technical Summary
Problems solved by technology
Method used
Image
Examples
Embodiment Construction
[0031] The present invention will be further described below in conjunction with accompanying drawing, protection scope of the present invention is not limited to the following:
[0032] Such as Figure 1-8 Shown: the testing device for the support mechanism of the drilling traction robot, which includes a support baffle (1), tension and pressure sensor A (2), tension and pressure sensor B (12), tension and pressure sensor C (9), tension and pressure sensor D (23 ), hydraulic pressure A (3), hydraulic pressure B (11), hydraulic pressure C (7), hydraulic pressure D (22), displacement sensor A (13), displacement sensor B (6), simulated shaft (4), support rod (5 ), bottom plate (8), telescopic rod (10), telescopic baffle (14), axial thrust bearing (15), support / torque baffle (16), slider A (201 / 202), slider B ( 181 / 182), support block A (21), support block B (17), connecting rod support mechanism (191), wedge support mechanism (192). The left support plate (401) and the right sup...
PUM
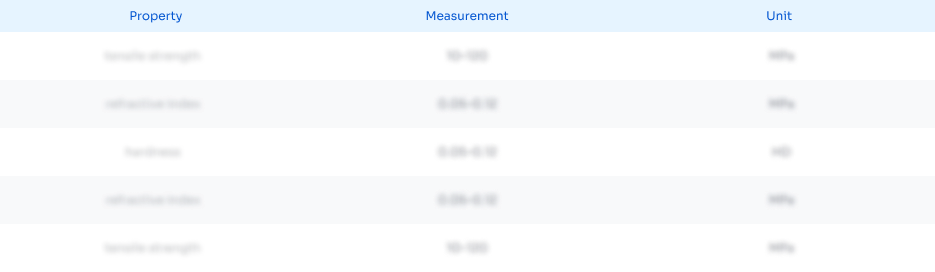
Abstract
Description
Claims
Application Information

- R&D
- Intellectual Property
- Life Sciences
- Materials
- Tech Scout
- Unparalleled Data Quality
- Higher Quality Content
- 60% Fewer Hallucinations
Browse by: Latest US Patents, China's latest patents, Technical Efficacy Thesaurus, Application Domain, Technology Topic, Popular Technical Reports.
© 2025 PatSnap. All rights reserved.Legal|Privacy policy|Modern Slavery Act Transparency Statement|Sitemap|About US| Contact US: help@patsnap.com