Treatment process for rotary kiln tail gas dust removal and denitration
A technology of tail gas dust removal and rotary kiln, which is applied in the fields of dispersed particle filtration, dispersed particle separation, chemical instruments and methods, etc. Poisoning ability, simplification of treatment process, and the effect of improving efficiency
- Summary
- Abstract
- Description
- Claims
- Application Information
AI Technical Summary
Problems solved by technology
Method used
Image
Examples
Embodiment Construction
[0026] The invention relates to a treatment process for dust removal and denitrification of tail gas of a rotary kiln.
[0027] The following will clearly and completely describe the technical solutions in the embodiments of the present invention with reference to the accompanying drawings in the embodiments of the present invention. Obviously, the described embodiments are only part of the embodiments of the present invention, not all of them. Based on the embodiments of the present invention, all other embodiments obtained by persons of ordinary skill in the art without making creative efforts fall within the protection scope of the present invention.
[0028] see figure 2 , image 3 , according to the process flow chart of rotary kiln tail gas denitrification and dust removal treatment of the present invention, specifically:
[0029] The high-temperature flue gas (temperature about 1000°C) coming out of the rotary kiln 1 kiln tail first enters the preheater 2 to preheat ...
PUM
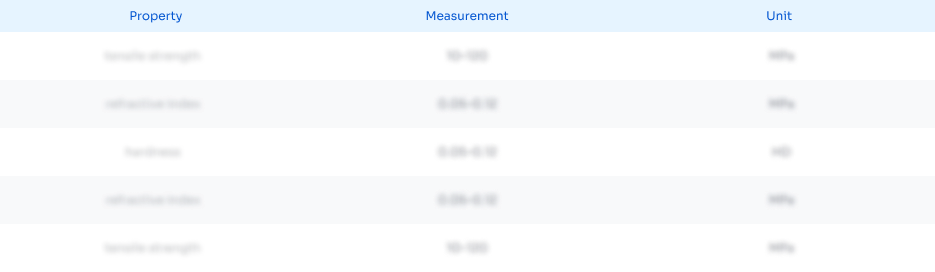
Abstract
Description
Claims
Application Information

- R&D Engineer
- R&D Manager
- IP Professional
- Industry Leading Data Capabilities
- Powerful AI technology
- Patent DNA Extraction
Browse by: Latest US Patents, China's latest patents, Technical Efficacy Thesaurus, Application Domain, Technology Topic, Popular Technical Reports.
© 2024 PatSnap. All rights reserved.Legal|Privacy policy|Modern Slavery Act Transparency Statement|Sitemap|About US| Contact US: help@patsnap.com