Design method of thick-wall part optical system comprising diffusion hole for eliminating dark area at chamfer
A design method and optical system technology, applied in optics, optical components, instruments, etc., can solve problems such as unevenness and dark areas
- Summary
- Abstract
- Description
- Claims
- Application Information
AI Technical Summary
Problems solved by technology
Method used
Image
Examples
Embodiment 1
[0050] This embodiment provides a design method for thick-walled parts including primary collimation and secondary collimation.
[0051] 1.( Figure 1 ~ Figure 4 As shown) After getting the customer's car light shape input, the width s of a single collimator can be determined by the width of the thick-walled part and the number of light sources given by the customer (s=width of the thick-walled part / number of light sources); as everything The position D of the light source 1 of the initially selected reference of the design, the side wall 2 that can be obtained according to the focal length and the light source position D, and the width t of the primary collimation structure of the thick-walled part, in the design principle and method of the present invention, By default, the width s of a single collimator, the position of the light source D, the side wall 2, and the width t of the primary collimation structure of thick-walled parts are known parameters. The maximum vertical ...
Embodiment 2
[0082] This embodiment provides a design method for a thick-walled part that does not include primary collimation but only has secondary collimation. The overall design principles and steps are the same as those of the above-mentioned thick-walled part that includes primary collimation and secondary collimation. , the different concepts are described as follows:
[0083] Such as Figure 20 As shown, different from the first article of the thick-walled part that includes primary and secondary collimation, this case defaults to known parameters including a single collimator width s, light source position D, and side wall 2, excluding primary Align thick wall part width.
[0084] The position of the light source 1, which is the initially selected reference for all designs, is the actual position, and there is no need to use the concept of virtual focus.
[0085] Scaling is not required in the design (including theoretical design and design of fine-tuning after entering the simu...
Embodiment 3
[0087] Such as Figure 24 , this embodiment provides a design method of designing the collimation surface of the prior art as a diffusion surface at the primary collimation. The primary collimation is aimed at the concept of light entering the medium from air through the optical surface and the optical structure using this concept , the design principle and method of the diffusion surface of the primary collimation are essentially the same as the design principle and method of the diffusion surface of the diffusion hole in the secondary collimation, and will not be described in detail here, only a few differences are mentioned here and note:
[0088] During the design process, the spherical surface 6b at point A corresponding to the above-mentioned secondary collimation is the spherical surface 12d in the primary collimation, and theoretically the position of 12d should be the same as Figure 24 12d in is a spherical arc that is offset in parallel and passes through point W, ...
PUM
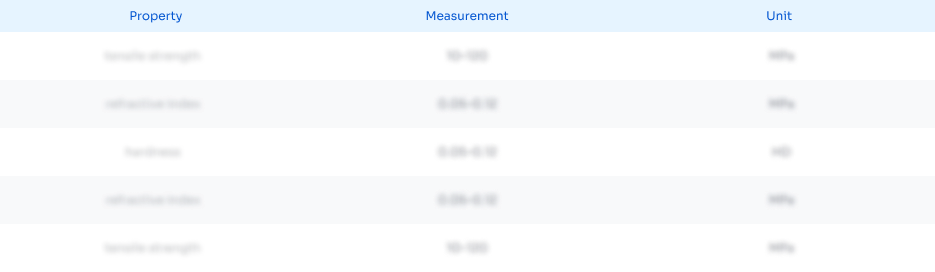
Abstract
Description
Claims
Application Information

- R&D Engineer
- R&D Manager
- IP Professional
- Industry Leading Data Capabilities
- Powerful AI technology
- Patent DNA Extraction
Browse by: Latest US Patents, China's latest patents, Technical Efficacy Thesaurus, Application Domain, Technology Topic.
© 2024 PatSnap. All rights reserved.Legal|Privacy policy|Modern Slavery Act Transparency Statement|Sitemap