Optical fiber and end cap automatic aligning and welding device and method based on optical power feedback
An automatic alignment and fiber end technology, which is applied in the field of optical communication, can solve the problems of reduced transmission efficiency, low alignment efficiency of optical fiber and glass end cap, and inability to improve welding efficiency, etc., to achieve complete device structure, improve welding efficiency, and improve alignment. The effect of quasi-precision
- Summary
- Abstract
- Description
- Claims
- Application Information
AI Technical Summary
Problems solved by technology
Method used
Image
Examples
Embodiment 1
[0033] Such as figure 1 As shown, the embodiment of the present invention provides a fiber end cap automatic alignment fusion splicing device based on optical power feedback, including:
[0034] Flame injection unit 1, lower clamp unit 2, upper clamp unit 3, position monitoring unit 4, optical power detection unit 5 and installation platform 6; the upper clamp unit 3 is provided with an upper clamp motion platform and an optical fiber clamp, and the optical fiber clamp It is arranged downwards on the upper clamp moving platform, and the optical fiber clamp is used to clamp the optical fiber; the lower clamp unit 2 is provided with a lower clamp moving platform and an end cap clamp, and the end cap clamp is used to clamp the glass end cap, the end cap clamp is arranged below the optical fiber clamp through the lower clamp motion platform; the position monitoring unit 4 is provided with a first position monitoring device and a second position monitoring device, and the first pos...
Embodiment 2
[0049] Such as Figure 7 As shown, the embodiment of the present invention provides a method for automatic alignment and fusion splicing of optical fiber end caps based on optical power feedback, including:
[0050] Step 1, loading the device, installing the optical fiber and the glass end cap on the optical fiber clamp and the end cap clamp respectively; the optical fiber needs to be installed in the optical fiber groove, and fixed on the optical fiber holding plate 309 by closing the optical fiber cover plate 310; the glass The end cap is installed between the clamp slider 208 and the first fixture seat 206, and the adjusting bolt 210 is rotated so that the clamping groove clamps the glass end cap; the end of the optical fiber is connected to the optical power meter;
[0051] Step 2, the optical fiber is aligned with the glass end cap, the upper fixture moving platform will drive the displacement of the optical fiber fixture through the upper fixture rotating platform 304 an...
PUM
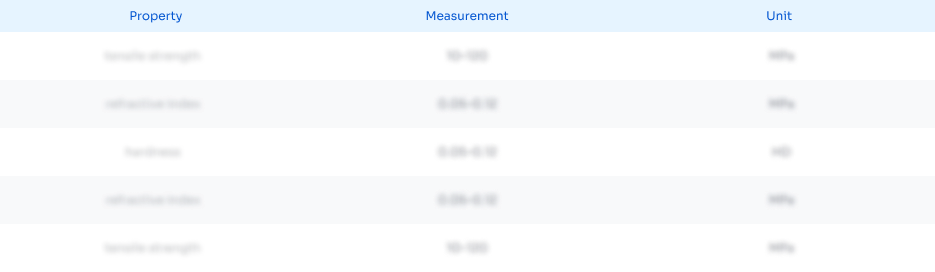
Abstract
Description
Claims
Application Information

- R&D
- Intellectual Property
- Life Sciences
- Materials
- Tech Scout
- Unparalleled Data Quality
- Higher Quality Content
- 60% Fewer Hallucinations
Browse by: Latest US Patents, China's latest patents, Technical Efficacy Thesaurus, Application Domain, Technology Topic, Popular Technical Reports.
© 2025 PatSnap. All rights reserved.Legal|Privacy policy|Modern Slavery Act Transparency Statement|Sitemap|About US| Contact US: help@patsnap.com