An automatic handling robot system, control method and storage device
A technology for handling robots and robots. It is applied in the direction of lifting equipment safety devices and lifting devices. It can solve the problems of inconvenient layout and expansion, failure to meet the needs of automatic pallet handling in factories, and labor-intensive problems, so as to achieve the effect of easy deployment and use.
- Summary
- Abstract
- Description
- Claims
- Application Information
AI Technical Summary
Problems solved by technology
Method used
Image
Examples
Embodiment 1
[0067] Such as figure 1 As shown, Embodiment 1 of the present invention provides an automatic handling robot system, including a robot body 2 and a fork body 1, the robot body 2 is connected to the fork body 1, and the robot body 2 includes a sensor system 20 , a power system 22, a control system 21, the fork body 1 includes a lifting system 11, a drive system 12;
[0068] The sensor system 20 is installed on the robot car body 2, the control system 21 reads the environmental information scanned by the sensor system 20, calculates the navigation driving path, and controls the movement of the drive system 12,
[0069] The control system 21 is connected to the power system 22 to control the movement of the power system 22, and the power system 22 provides power for the connection of the lifting system 11,
[0070] Such as Figure 4 As shown, the fork body 1 also includes a measurement sensor 13. It should be noted that the measurement sensor 13 can be a laser sensor, a camera,...
Embodiment 2
[0089] Such as Figure 10 As shown, the embodiment of the present invention also provides a method for controlling an automatic handling robot, including the following steps:
[0090] Step S1: Issue task instructions to the task dispatching unit of the control system through the operation terminal, including the picking station and the unloading station;
[0091] Step S2: the navigation control unit reads the environmental information scanned by the sensor system;
[0092] Step S3: The task scheduling unit issues tasks to the navigation control unit according to the information of the reclaiming site, and the internal navigation algorithm calculates the navigation route from the starting point to the reclaiming site;
[0093] Step S4: The task scheduling unit issues a signal to the drive control unit according to the navigation route, and the drive control unit controls the movement of the drive system according to the navigation route;
[0094] Step S5: The robot travels to...
PUM
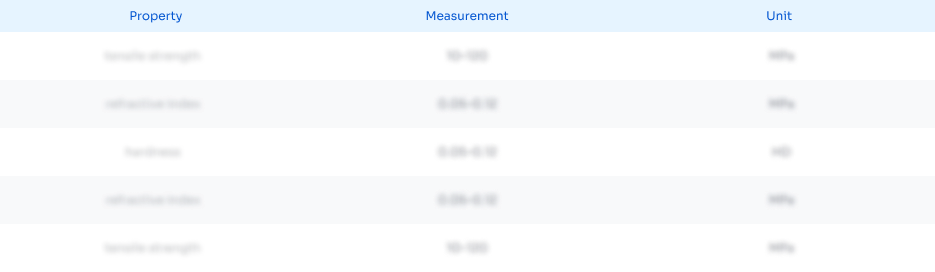
Abstract
Description
Claims
Application Information

- R&D
- Intellectual Property
- Life Sciences
- Materials
- Tech Scout
- Unparalleled Data Quality
- Higher Quality Content
- 60% Fewer Hallucinations
Browse by: Latest US Patents, China's latest patents, Technical Efficacy Thesaurus, Application Domain, Technology Topic, Popular Technical Reports.
© 2025 PatSnap. All rights reserved.Legal|Privacy policy|Modern Slavery Act Transparency Statement|Sitemap|About US| Contact US: help@patsnap.com