Unconstrained mobile soft-body robot and driving method thereof
A driving method and unconstrained technology, applied in manipulators, program-controlled manipulators, manufacturing tools, etc., can solve the problems of unfavorable miniaturization, light weight and convenience of soft robots, and increase the weight of soft robots, so as to improve driving efficiency and reduce small size effect
- Summary
- Abstract
- Description
- Claims
- Application Information
AI Technical Summary
Problems solved by technology
Method used
Image
Examples
Embodiment Construction
[0033] The present invention will be further described below in conjunction with accompanying drawing.
[0034] Such as figure 1 As shown, an unconstrained mobile soft robot includes a front shell 1-1, a rear shell 1-2, a driver 2, a one-way bearing wheel 3 and an integrated circuit substrate 4. The front outer casing 1-1 and the rear outer casing 1-2 are connected together by two drivers 2 arranged side by side, and serve as the head and the tail of the soft robot respectively. One-way bearing wheels 3 are installed on both sides of the front-end outer casing 1-1 and the rear-end outer casing 1-2. The one-way bearing wheel 3 is obtained by installing a tire bead on the outer ring of the one-way bearing, and can only rotate forwardly so that the front end casing 1-1 or the rear end casing 1-2 advances, but cannot reverse.
[0035] Such as figure 2 with 3 As shown, the driver 2 is in the shape of a strip and is composed of M driving units stacked one after the other, where...
PUM
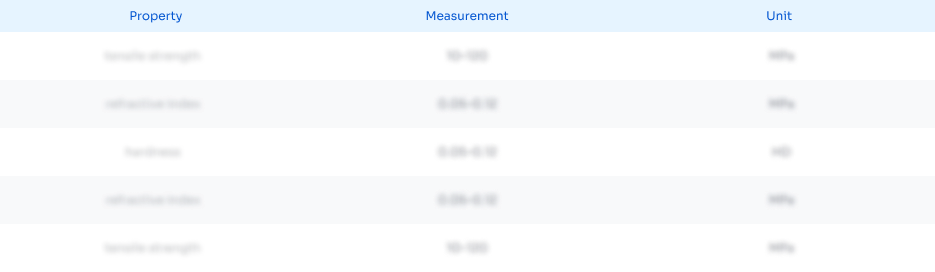
Abstract
Description
Claims
Application Information

- R&D
- Intellectual Property
- Life Sciences
- Materials
- Tech Scout
- Unparalleled Data Quality
- Higher Quality Content
- 60% Fewer Hallucinations
Browse by: Latest US Patents, China's latest patents, Technical Efficacy Thesaurus, Application Domain, Technology Topic, Popular Technical Reports.
© 2025 PatSnap. All rights reserved.Legal|Privacy policy|Modern Slavery Act Transparency Statement|Sitemap|About US| Contact US: help@patsnap.com