Zoom camera calibration method
A zoom camera and calibration method technology, which is applied in the field of camera calibration in machine vision, can solve the problems of large range of shooting distance and difficult to use
- Summary
- Abstract
- Description
- Claims
- Application Information
AI Technical Summary
Problems solved by technology
Method used
Image
Examples
Embodiment Construction
[0074] The present invention will be further described below in conjunction with the accompanying drawings and specific embodiments.
[0075] The present invention adopts the scheme of camera principal point position and focal length separation calibration. Firstly, the principal point position of the camera is calibrated, and then based on this, the focal length of the zoom camera is calibrated at different camera lens group positions.
[0076] Calibration of the principal point position of the zoom camera:
[0077] 1. The calibration steps of the principal point position of the zoom camera are as follows:
[0078] 1) Fix the position of the camera, only adjust the focal length of the camera, and always keep the camera focused to infinity, and shoot several calibration images.
[0079] 2) Use the Sift feature extraction algorithm to perform feature point extraction and preliminary matching on each image.
[0080] 3) Accurate matches are obtained using a random sampling con...
PUM
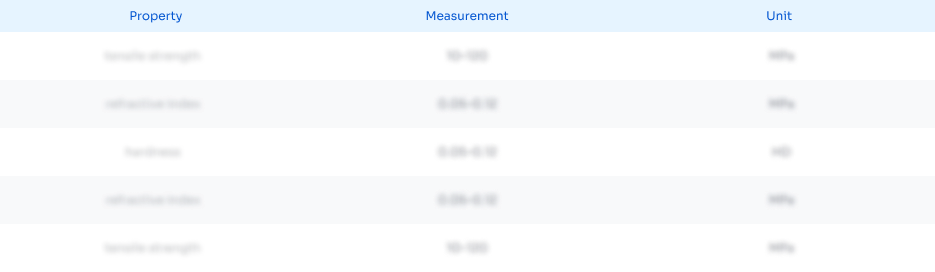
Abstract
Description
Claims
Application Information

- R&D
- Intellectual Property
- Life Sciences
- Materials
- Tech Scout
- Unparalleled Data Quality
- Higher Quality Content
- 60% Fewer Hallucinations
Browse by: Latest US Patents, China's latest patents, Technical Efficacy Thesaurus, Application Domain, Technology Topic, Popular Technical Reports.
© 2025 PatSnap. All rights reserved.Legal|Privacy policy|Modern Slavery Act Transparency Statement|Sitemap|About US| Contact US: help@patsnap.com