Temperature difference assembly part, assembly method and light rigid body assembly with temperature difference assembly part
A temperature difference and component technology, applied in the field of temperature difference assembly components, can solve problems such as short circuits, changes in metal properties, risks, etc., and achieve the effects of rapid assembly and disassembly, greatly reduced material preparation costs, and increased flexibility
- Summary
- Abstract
- Description
- Claims
- Application Information
AI Technical Summary
Problems solved by technology
Method used
Image
Examples
Embodiment Construction
[0031] The present invention will be further elaborated below in conjunction with the accompanying drawings and specific embodiments. These examples should be understood as only for illustrating the present invention but not for limiting the protection scope of the present invention. After reading the contents of the present invention, those skilled in the art can make various changes or modifications to the present invention, and these equivalent changes and modifications also fall within the scope defined by the claims of the present invention.
[0032] Figure 1 to Figure 3 It is a schematic diagram and a perspective view of the first preferred embodiment of the temperature difference assembly member of the present invention, the subject 11 is in the shape of a long straight cylinder, has a subject 111 and a subject 112 extending from the subject 111, and the surface of the subject 112 is formed with low heat Transfer layer 13, low heat transfer layer 13 belongs to high th...
PUM
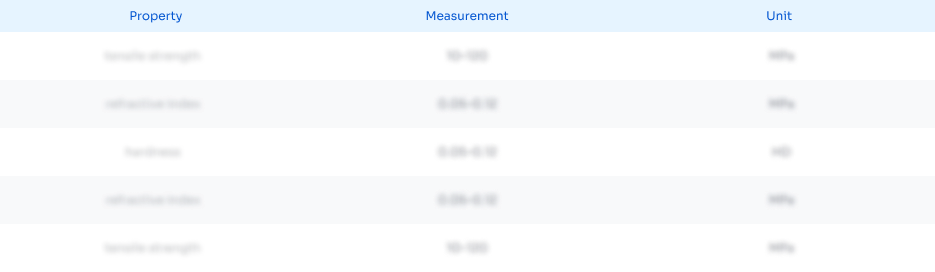
Abstract
Description
Claims
Application Information

- Generate Ideas
- Intellectual Property
- Life Sciences
- Materials
- Tech Scout
- Unparalleled Data Quality
- Higher Quality Content
- 60% Fewer Hallucinations
Browse by: Latest US Patents, China's latest patents, Technical Efficacy Thesaurus, Application Domain, Technology Topic, Popular Technical Reports.
© 2025 PatSnap. All rights reserved.Legal|Privacy policy|Modern Slavery Act Transparency Statement|Sitemap|About US| Contact US: help@patsnap.com