Buffeting-free sliding mode control method of piezoelectric driving micro-positioning platform
A micro-positioning platform, piezoelectric drive technology, applied in the field of control, can solve problems such as severe switching chattering, affecting control performance and engineering applications, and achieve the effects of fast response speed, improved order, and high control accuracy
- Summary
- Abstract
- Description
- Claims
- Application Information
AI Technical Summary
Problems solved by technology
Method used
Image
Examples
Embodiment Construction
[0029] The invention provides a chatter-free sliding mode control method for a piezoelectric driven micro-positioning platform. The state relation equation is derived by establishing a Duhem-based piezoelectric driven micro-positioning platform system model with unknown disturbances, and a proportional-integral sliding mode surface is designed. And disturbance estimator, and based on the proportional-integral sliding mode surface and disturbance estimator, a kind of chatter-free equivalent sliding mode controller is designed to control the piezoelectric driven micro-positioning platform. The control method has strong robustness and control accuracy. Higher and faster response speed is conducive to engineering practice.
[0030] The design steps of the chatter-free sliding mode controller of the present invention:
[0031] Step Q1, consider the unknown disturbance parts such as internal unmodeled dynamics, parameter uncertainties and external disturbance variables, establish a piezo...
PUM
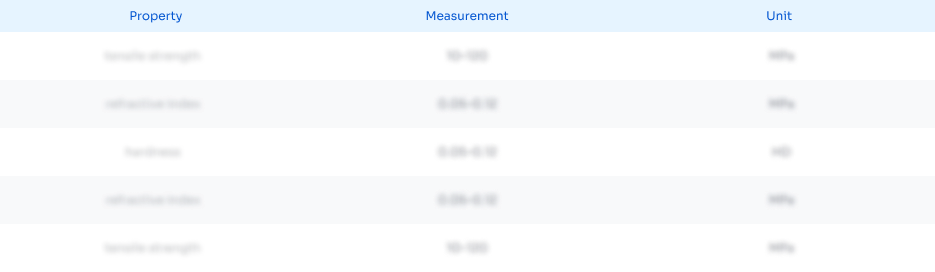
Abstract
Description
Claims
Application Information

- Generate Ideas
- Intellectual Property
- Life Sciences
- Materials
- Tech Scout
- Unparalleled Data Quality
- Higher Quality Content
- 60% Fewer Hallucinations
Browse by: Latest US Patents, China's latest patents, Technical Efficacy Thesaurus, Application Domain, Technology Topic, Popular Technical Reports.
© 2025 PatSnap. All rights reserved.Legal|Privacy policy|Modern Slavery Act Transparency Statement|Sitemap|About US| Contact US: help@patsnap.com