Robot collision detection system and method based on neural network
A technology of collision detection and neural network, which is applied in the field of robot collision detection system based on neural network, can solve the problems of large amount of visual sensor data, the accuracy of observation is not as good as the actual measurement of the sensor, and increase the cost of the system, so as to achieve high and excellent collision detection accuracy The effect of generalization ability and concise algorithm
- Summary
- Abstract
- Description
- Claims
- Application Information
AI Technical Summary
Problems solved by technology
Method used
Image
Examples
Embodiment Construction
[0063] In order to make the object, technical solution and advantages of the present invention clearer, the present invention will be further described in detail below in combination with specific embodiments and with reference to the accompanying drawings. It should be understood that these descriptions are exemplary only, and are not intended to limit the scope of the present invention. Also, in the following description, descriptions of well-known structures and techniques are omitted to avoid unnecessarily obscuring the concept of the present invention.
[0064] The invention proposes a robot collision detection scheme based on a neural network. Specifically, the neural network is used to predict the current position of the robot’s servo motor based on the robot’s command information and feedback state information, and compare the difference with the actual position of the robot’s servo motor. When the deviation exceeds a certain threshold, it is determined that the robot ...
PUM
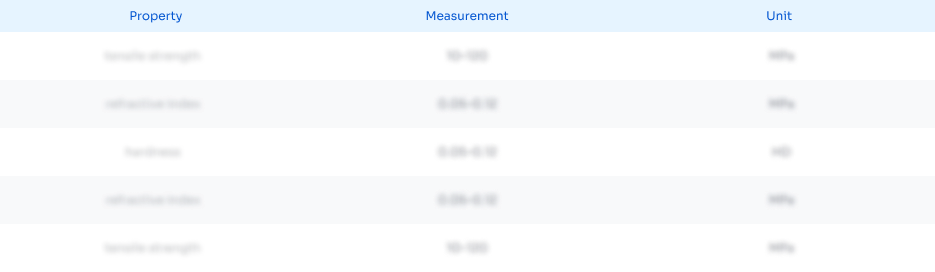
Abstract
Description
Claims
Application Information

- Generate Ideas
- Intellectual Property
- Life Sciences
- Materials
- Tech Scout
- Unparalleled Data Quality
- Higher Quality Content
- 60% Fewer Hallucinations
Browse by: Latest US Patents, China's latest patents, Technical Efficacy Thesaurus, Application Domain, Technology Topic, Popular Technical Reports.
© 2025 PatSnap. All rights reserved.Legal|Privacy policy|Modern Slavery Act Transparency Statement|Sitemap|About US| Contact US: help@patsnap.com