Built-in distributed full three-dimensional continuous micro-flow high-energy sound wave high-efficiency and energy-saving cleaning system
A high-efficiency and energy-saving technology for sonic cleaning
- Summary
- Abstract
- Description
- Claims
- Application Information
AI Technical Summary
Problems solved by technology
Method used
Image
Examples
Embodiment Construction
[0022] like Figure 4 As shown, the built-in distributed full-stereo continuous micro-flow high-energy sound wave high-efficiency and energy-saving dust cleaning system in this embodiment includes a resonant cavity type acoustic wave dust remover 100, a pulse resonance cavity composite acoustic wave dust remover 200, a pulse type acoustic wave dust remover 300 and A distributed full stereo sonic cleaning unit composed of compressed gas pipeline 400, the resonant cavity type sonic cleaner 100, the pulse resonant cavity composite sonic cleaner 200 and the pulsed sonic soot cleaner 300 ; The distributed full stereo wave ash cleaning unit is installed at intervals on the compressed gas pipeline 400 . In each of the distributed full stereo sound wave cleaning units: the air inlet of the resonant cavity type sonic cleaner 100, the air inlet of the pulse resonant cavity composite sonic cleaner 200 and the pulse The air inlet of the type acoustic wave dust cleaner 300 is in fluid com...
PUM
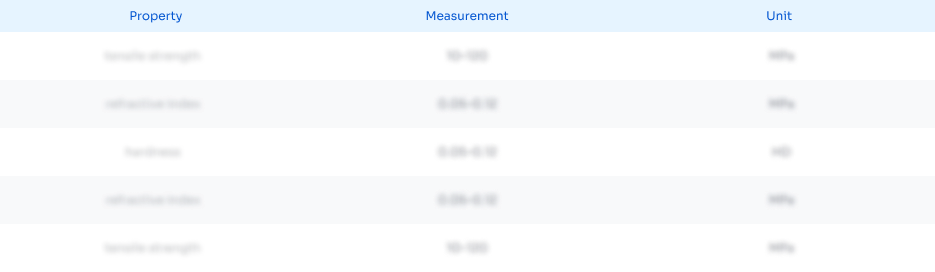
Abstract
Description
Claims
Application Information

- R&D
- Intellectual Property
- Life Sciences
- Materials
- Tech Scout
- Unparalleled Data Quality
- Higher Quality Content
- 60% Fewer Hallucinations
Browse by: Latest US Patents, China's latest patents, Technical Efficacy Thesaurus, Application Domain, Technology Topic, Popular Technical Reports.
© 2025 PatSnap. All rights reserved.Legal|Privacy policy|Modern Slavery Act Transparency Statement|Sitemap|About US| Contact US: help@patsnap.com