3D printing sand core structure for rapidly developing cylinder cover casting and manufacturing method thereof
A 3D printing and cylinder head technology, applied in the direction of casting mold, core, casting mold composition, etc., can solve the problems of high investment, difficult development, long cycle, etc., and achieve low manufacturing difficulty, reduce development difficulty, and short cycle Effect
- Summary
- Abstract
- Description
- Claims
- Application Information
AI Technical Summary
Problems solved by technology
Method used
Image
Examples
Embodiment Construction
[0029] In order to more clearly illustrate the technical solutions in the embodiments of the present invention or the prior art, the following will briefly introduce the drawings that need to be used in the description of the embodiments or the prior art. Obviously, the accompanying drawings in the following description are only These are some embodiments of the present invention. Those skilled in the art can also obtain other drawings based on these drawings without creative work.
[0030] Such as figure 2 As shown, the molding of traditional cylinder head castings requires at least 8 types of sand cores, upper water jacket sand core 1, lower water jacket sand core 2, intake port sand core 3, exhaust port sand core 4, top cover sand core 5. Upper side sand core 6-1 and upper side sand core 6-2, bottom plate sand core 7, lower side sand core 8-1 and lower side sand core 8-2. Among them, the upper water jacket sand core 1, the lower water jacket sand core 2, the air inlet san...
PUM
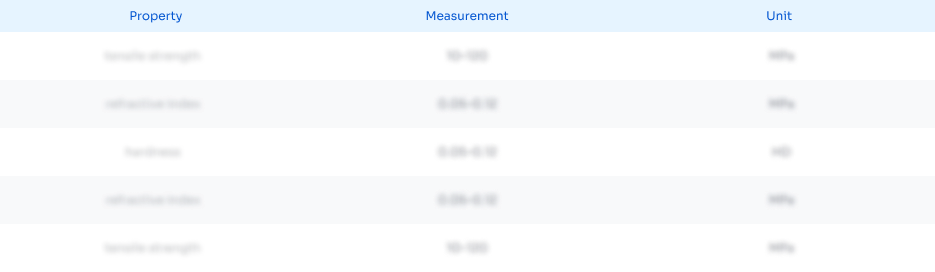
Abstract
Description
Claims
Application Information

- R&D Engineer
- R&D Manager
- IP Professional
- Industry Leading Data Capabilities
- Powerful AI technology
- Patent DNA Extraction
Browse by: Latest US Patents, China's latest patents, Technical Efficacy Thesaurus, Application Domain, Technology Topic, Popular Technical Reports.
© 2024 PatSnap. All rights reserved.Legal|Privacy policy|Modern Slavery Act Transparency Statement|Sitemap|About US| Contact US: help@patsnap.com