Self-adaptive high-order vibration active control method for mechanical refrigerator
A mechanical refrigeration and active control technology, applied in mechanical oscillation control, non-electric variable control, household refrigeration equipment, etc., can solve problems such as sensor interference, imaging blur, interference, etc., achieve good convergence and robustness, and satisfy multiple requirements Effect of order noise, wide application space
- Summary
- Abstract
- Description
- Claims
- Application Information
AI Technical Summary
Problems solved by technology
Method used
Image
Examples
Embodiment Construction
[0050] The specific content of the present invention will be further described below in conjunction with the accompanying drawings, but the specific embodiments of the present invention are not limited thereto. All those that realize the functions of the present invention according to the inventive spirit, characteristics, modes and functions of the present invention are within the protection scope of the present invention.
[0051] refer to figure 1 As shown, the present invention is realized through the following technical solutions: a method for adaptive high-order active vibration control of a mechanical refrigerator, and the active vibration control method includes the following steps:
[0052] (1) Output the drive control signal x(n) to two opposing linear motors in the mechanical refrigerator.
[0053] (2) x(n) is used as a reference signal to collect the initial vibration signal e(n), which is input to a controller integrated with an adaptive high-order vibration acti...
PUM
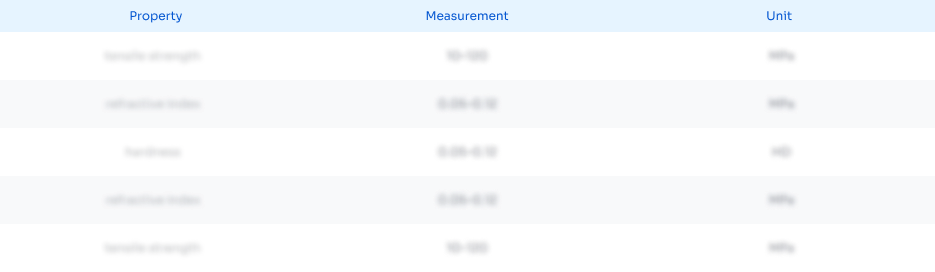
Abstract
Description
Claims
Application Information

- R&D
- Intellectual Property
- Life Sciences
- Materials
- Tech Scout
- Unparalleled Data Quality
- Higher Quality Content
- 60% Fewer Hallucinations
Browse by: Latest US Patents, China's latest patents, Technical Efficacy Thesaurus, Application Domain, Technology Topic, Popular Technical Reports.
© 2025 PatSnap. All rights reserved.Legal|Privacy policy|Modern Slavery Act Transparency Statement|Sitemap|About US| Contact US: help@patsnap.com