Connecting structure suitable for missile launcher loading
A missile launcher and connection structure technology, which is applied in the direction of the launch device, connection, and parts of the connection device, can solve the problems of low efficiency of large-diameter cables, large diameter of launch cables, and affecting loading efficiency, so as to save loading time, The effect of improving installation efficiency and improving loading efficiency
- Summary
- Abstract
- Description
- Claims
- Application Information
AI Technical Summary
Problems solved by technology
Method used
Image
Examples
Embodiment Construction
[0041] The present invention will be described in detail below in conjunction with specific embodiments. The following examples will help those skilled in the art to further understand the present invention, but do not limit the present invention in any form. It should be noted that those skilled in the art can make several changes and improvements without departing from the concept of the present invention. These all belong to the protection scope of the present invention.
[0042] The invention provides a connection structure suitable for loading missile launchers, such as Figure 1-4 As shown, it includes a missile joint installation module 1, a missile launcher 2 and a vehicle-mounted launch control cable. The missile joint installation module 1 is provided with a joint installation rack cable 13, and the missile joint installation module 1 is installed on the missile launcher 2. In addition, the connecting rack cable 13 can be connected with the vehicle-mounted launch c...
PUM
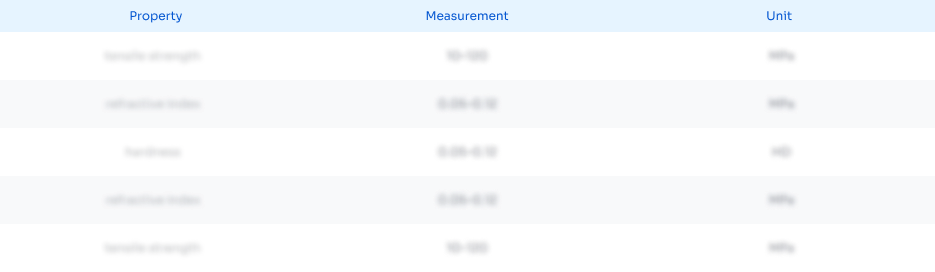
Abstract
Description
Claims
Application Information

- R&D Engineer
- R&D Manager
- IP Professional
- Industry Leading Data Capabilities
- Powerful AI technology
- Patent DNA Extraction
Browse by: Latest US Patents, China's latest patents, Technical Efficacy Thesaurus, Application Domain, Technology Topic, Popular Technical Reports.
© 2024 PatSnap. All rights reserved.Legal|Privacy policy|Modern Slavery Act Transparency Statement|Sitemap|About US| Contact US: help@patsnap.com