Storage battery plate and drying process and device thereof
A drying process and storage battery technology, applied in the direction of lead-acid battery electrodes, etc., can solve the problems of long curing time and high energy consumption
- Summary
- Abstract
- Description
- Claims
- Application Information
AI Technical Summary
Problems solved by technology
Method used
Image
Examples
Embodiment Construction
[0023] The technical solutions of the present invention will be clearly and completely described below in conjunction with the accompanying drawings. Apparently, the described embodiments are part of the embodiments of the present invention, not all of them.
[0024] Step 1: Adjust the size of the air outlet (the gap between each air screen) of the air screen 2 in the curing room to ensure that the maximum wind speed difference at each position does not exceed 0.5m / S. The detailed data is shown in Table 1:
[0025] Table 1
[0026]
[0027] Step 2) Place the 100,000 pieces of wet plates 1 coated with lead paste in the curing room adjusted in step 1) for curing. After the wet raw plates 1 are cured, the moisture content of the wet plates 1 is 4.5%, and enter the drying stage .
[0028] Step 3) In the drying stage, adjust the curing indoor environment to a temperature of 85°C. At this time, close the air inlet door 3 and the air outlet door 4, and rely on the evaporation of ...
PUM
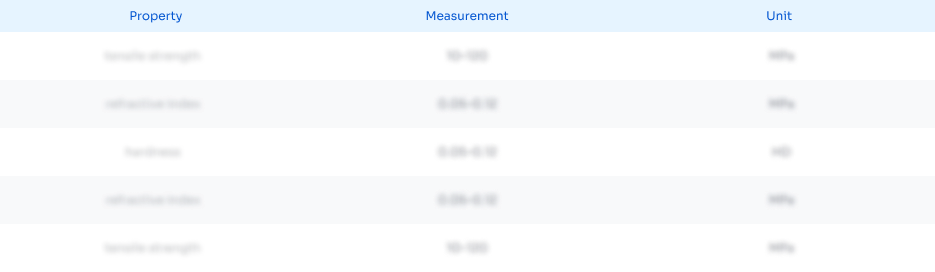
Abstract
Description
Claims
Application Information

- R&D Engineer
- R&D Manager
- IP Professional
- Industry Leading Data Capabilities
- Powerful AI technology
- Patent DNA Extraction
Browse by: Latest US Patents, China's latest patents, Technical Efficacy Thesaurus, Application Domain, Technology Topic, Popular Technical Reports.
© 2024 PatSnap. All rights reserved.Legal|Privacy policy|Modern Slavery Act Transparency Statement|Sitemap|About US| Contact US: help@patsnap.com