Feeding and blanking device
A technology of silo and mounting plate, which is applied in the field of loading and unloading devices, can solve the problems of being placed alone at the detection station, and achieve the effect of simple structure and convenient operation
- Summary
- Abstract
- Description
- Claims
- Application Information
AI Technical Summary
Problems solved by technology
Method used
Image
Examples
Embodiment 1
[0084] refer to Figure 1-3 , the present embodiment is to provide a loading and unloading device, which specifically includes a frame 10 and is located on the frame 10:
[0085] The first manipulator 20 is used to take the tray 200 on which the product 400 to be inspected is placed from the feeding device; at the same time, the tray 200 on which the product 400 has been inspected is placed back into the feeding device;
[0086] The bin device 30 is used to store the pallet 200 delivered by the first manipulator 20;
[0087] The second manipulator 40 is used to take out the product 400 to be tested from the pallet 200 of the bin device 30, and place it on the detection station 501 of the detection device 500; at the same time, the product 400 that has been detected is taken out by the detection station 501, Put back in the empty tray of feed bin device 30 again.
[0088] The loading and unloading device 100 provided in this embodiment first moves the product 400 and its tray...
Embodiment 2
[0100] This embodiment is to provide a bin device, which is mainly used in the loading and unloading device 100 provided in the first embodiment, and can put the tested products 400 back into the original tray 200 . Specifically, refer to Figure 4 , the silo device 30 includes:
[0101] The first bin 31 is used to place the tray 200 transported by the first manipulator 20 containing the product 400 to be inspected;
[0102] The second silo 32 is used to store the empty trays delivered by the first silo 31;
[0103] The third silo 33 is used to receive the empty trays delivered by the second silo 32 , and the products 400 that have been tested are put back into the original trays 200 in the third silo 33 .
[0104] Further, refer to image 3 with Figure 4 , the first silo 31, the second silo 32 and the third silo 33 are sequentially arranged linearly on the support plate 12, which not only facilitates the transfer of empty pallets between each other, but also compresses t...
Embodiment 3
[0138] For electronic products, due to their fine internal structure, in order to avoid damage caused by shaking during assembly and transportation, the electronic product 400 is usually loaded on the carrier 300, and then the carrier 300 is placed on the pallet 200 as a whole to ensure The product 400 is solid. Specifically, refer to Figure 10 and Figure 11 , a storage slot 304 is provided on the carrier 300, and the product 400 is placed in the storage slot 304; in order to prevent the product 400 from shaking, elastic claws 301 are provided on the side wall of the storage slot 304 to clamp the product 400 horizontally. After the product 400 is manufactured or the corresponding inspection is completed, the carrier 300 will no longer function, and the product 400 does not need to be put back into the carrier 300, but can be placed directly in the tray 200; and the carrier 300 can be collected uniformly for future use. The use of the next batch of products 400 , therefore,...
PUM
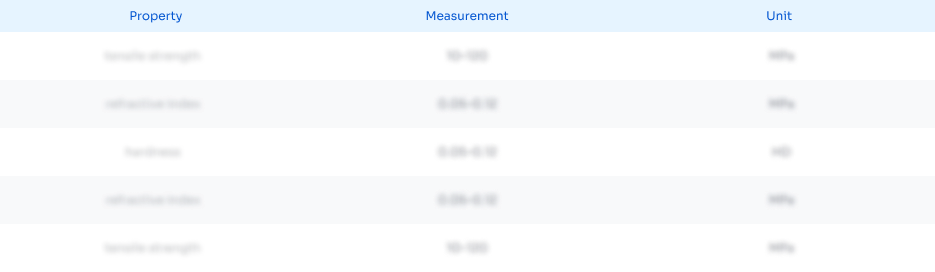
Abstract
Description
Claims
Application Information

- R&D
- Intellectual Property
- Life Sciences
- Materials
- Tech Scout
- Unparalleled Data Quality
- Higher Quality Content
- 60% Fewer Hallucinations
Browse by: Latest US Patents, China's latest patents, Technical Efficacy Thesaurus, Application Domain, Technology Topic, Popular Technical Reports.
© 2025 PatSnap. All rights reserved.Legal|Privacy policy|Modern Slavery Act Transparency Statement|Sitemap|About US| Contact US: help@patsnap.com