Screw-based nanometric linear motion control mechanism
A technology of linear motion and control mechanism, applied in the direction of piezoelectric effect/electrostrictive or magnetostrictive motor, generator/motor, transmission device, etc., can solve the problem of screw gap, wear and reduce the accuracy of the mechanism over time And other issues
- Summary
- Abstract
- Description
- Claims
- Application Information
AI Technical Summary
Problems solved by technology
Method used
Image
Examples
Embodiment Construction
[0055] refer to figure 1 and 2 , the translational motion control mechanism includes a rotor 1, also referred to as a rotor subassembly. The rotor 1 has a first end 3 with a first threaded portion 2 comprising a first thread. The first thread has a first pitch. The second end 5 of the rotor 1 has a second threaded portion 6 comprising a second thread with a second pitch that is the same as or different from the first pitch. figure 1 A first threaded part 2 and a second threaded part 6 are shown, each in the form of a rod with an external thread. figure 2 A first threaded part 2 and a second threaded part 6 are shown, each in the form of a rod with an internal thread or tap. Of course, it is possible to have the rotor 1 threaded at one end and tapped at the other end.
[0056] Between the first and second threaded parts 2 and 6 there is provided a central part 4 which defines an active area 7 of the rotor 1 . The active area 7 has an advantageously circular drive area 9 ...
PUM
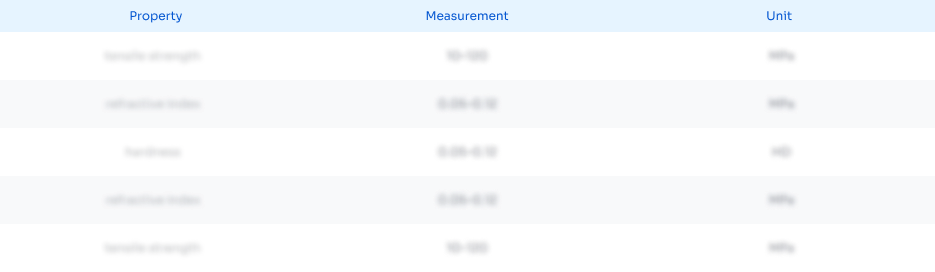
Abstract
Description
Claims
Application Information

- R&D
- Intellectual Property
- Life Sciences
- Materials
- Tech Scout
- Unparalleled Data Quality
- Higher Quality Content
- 60% Fewer Hallucinations
Browse by: Latest US Patents, China's latest patents, Technical Efficacy Thesaurus, Application Domain, Technology Topic, Popular Technical Reports.
© 2025 PatSnap. All rights reserved.Legal|Privacy policy|Modern Slavery Act Transparency Statement|Sitemap|About US| Contact US: help@patsnap.com