Automatic welding robot
A welding robot and automatic welding technology, applied in welding equipment, auxiliary welding equipment, welding/cutting auxiliary equipment, etc., can solve the problems of inconvenient pipe fixing, reduce welding efficiency, etc. Effect
- Summary
- Abstract
- Description
- Claims
- Application Information
AI Technical Summary
Problems solved by technology
Method used
Image
Examples
Embodiment 1
[0030] refer to Figure 1-5 , an automatic welding robot, including a base 1, the top of the base 1 is slidably connected with a welding robot body, the welding robot body includes a robot base 8 and a welding arm 10, and the top of the base 1 is slidably mounted with two fixed plates 5, two fixed plates The tops of 5 are fixedly equipped with support plates 6, and the sides of the two support plates 6 that are close to each other are rotatably connected with cylinders 12, and the two cylinders 12 are screwed with fixing bolts 32, and the two cylinders 12 are each Welded pipes 11 are movably connected, driving structures are fixedly connected to the two supporting plates 6, and the two cylinders 12 are respectively adapted to the two driving structures, and the tops of the two supporting plates 6 are fixedly connected to the dust suction cylinder 14 , the two dust suction cylinders 14 are provided with a dust suction structure, and the two dust suction structures are adapted t...
Embodiment 2
[0041] refer to Figure 1-5 , an automatic welding robot, including a base 1, the top of the base 1 is slidably connected with a welding robot body, the welding robot body includes a robot base 8 and a welding arm 10, and the top of the base 1 is slidably mounted with two fixed plates 5, two fixed plates The tops of 5 are all fixedly installed with support plates 6 by welding, and the sides of the two support plates 6 that are close to each other are rotatably connected with cylinders 12, and the two cylinders 12 are screwed with fixing bolts 32, and the two cylinders 12 Welded pipes 11 are movably connected inside, and the drive structure is fixedly connected to the two support plates 6 by screws. The two cylinders 12 are respectively adapted to the two drive structures, and the tops of the two support plates 6 are fixed by screws. A dust suction cylinder 14 is connected, and a dust suction structure is arranged inside the two dust suction cylinders 14, and the two dust sucti...
PUM
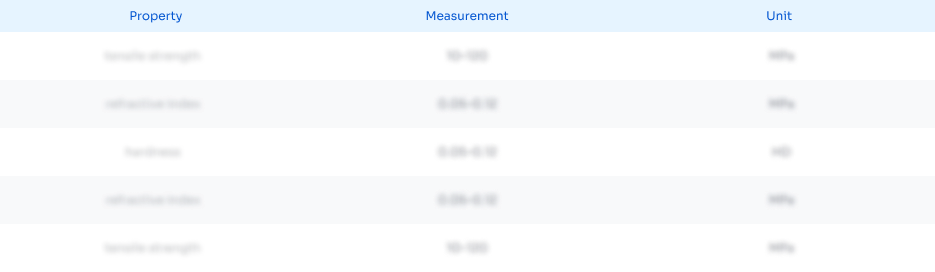
Abstract
Description
Claims
Application Information

- Generate Ideas
- Intellectual Property
- Life Sciences
- Materials
- Tech Scout
- Unparalleled Data Quality
- Higher Quality Content
- 60% Fewer Hallucinations
Browse by: Latest US Patents, China's latest patents, Technical Efficacy Thesaurus, Application Domain, Technology Topic, Popular Technical Reports.
© 2025 PatSnap. All rights reserved.Legal|Privacy policy|Modern Slavery Act Transparency Statement|Sitemap|About US| Contact US: help@patsnap.com