Molecular distillation system
A molecular distillation and distillation chamber technology, applied in molecular distillation and other directions, can solve the problems of poor theoretical value of distillation effect, no reuse, and low heating temperature, so as to reduce the energy consumption of heat dissipation, realize recycling, and increase fluidity. Effect
- Summary
- Abstract
- Description
- Claims
- Application Information
AI Technical Summary
Problems solved by technology
Method used
Image
Examples
Embodiment
[0024] Such as Figure 1-4 As shown, the present invention provides a technical solution: a molecular distillation system, including a screw extruder 1, a feed pipe 2, a distillation chamber 3, a connecting pipe 4, a light medium storage tank 5, a heavy medium storage tank 6 and heat dissipation Box 7, screw extruder 1 and distillation chamber 3 are connected by feed pipe 2. The outer wall of feed pipe 2 is sleeved with coil 201, distillation chamber 3 includes distillation tank 301, and the outer wall of distillation tank 301 is provided with heating clamps. Cover 302, the top and bottom of the distillation tank 301 are respectively fixed with a top cover 303 and a base 310 by bolts, the top of the top cover 303 is provided with a feed pipe 304, the feed pipe 304 is connected with the feed pipe 2, and the top center of the top cover 303 The motor 305 is fixed by bolts, and the bottom of the motor 305 is connected with a drive shaft 306, the bottom of the drive shaft 306 is sle...
PUM
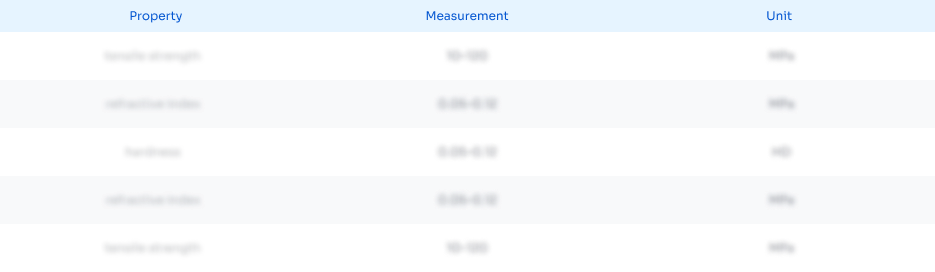
Abstract
Description
Claims
Application Information

- Generate Ideas
- Intellectual Property
- Life Sciences
- Materials
- Tech Scout
- Unparalleled Data Quality
- Higher Quality Content
- 60% Fewer Hallucinations
Browse by: Latest US Patents, China's latest patents, Technical Efficacy Thesaurus, Application Domain, Technology Topic, Popular Technical Reports.
© 2025 PatSnap. All rights reserved.Legal|Privacy policy|Modern Slavery Act Transparency Statement|Sitemap|About US| Contact US: help@patsnap.com