Installation parameter calibration device and method for visual tracking assembly
A visual tracking and component installation technology, applied in the field of motion tracking, can solve problems such as failure to meet calibration conditions, failure to consider target installation errors, failure to consider and eliminate unknown or unmodeled error sources, etc., to improve calibration accuracy and improve Tracking accuracy, effects of removing unknown or unmodeled errors
- Summary
- Abstract
- Description
- Claims
- Application Information
AI Technical Summary
Problems solved by technology
Method used
Image
Examples
Embodiment 1
[0054] A calibration device for installation parameters of visual tracking components:
[0055] The device includes a camera mounting bracket 1, a target mounting bracket 2, a two-dimensional turntable 3, a data acquisition module 4, and a calibration computer 5.
[0056] The camera mounting bracket 1 is used to fix the tracking camera so that its optical axis faces a proper direction in the fixed reference coordinate system;
[0057] Several sets of targets are installed on the tracked target, the tracked target is fixed on the two-dimensional turntable 3 through the target mounting bracket 2, and the two-dimensional turntable 3 is fixedly installed in a fixed reference coordinate system;
[0058] The data collection module 4 is used to collect the posture data of the two-dimensional turntable and the posture data output by the visual tracking system;
[0059] The calibration computer 5 is used to control the rotation posture of the two-dimensional turntable 3, receive the data collect...
Embodiment 2
[0061] The method of using the above-mentioned calibration device to calibrate the installation parameters of the visual tracking component is as follows:
[0062] Fix the tracking camera at the normal working position of the environment through the mounting bracket 1, fix the two-dimensional turntable 3 at the center of the normal working range of the environment where the tracked target is located, and fix the tracked target at the second position through the mounting bracket 2. On the dimensional turntable 3, the camera can image the target on the target within a certain movement range of the target.
[0063] Control the two-dimensional turntable 3 to rotate N positions so that the camera can image each group of targets on the target. At each rotation position of the two-dimensional turntable 3, use the data acquisition module 4 to collect the posture data and vision output by the two-dimensional turntable 3 The posture data output by the tracking system, as the two-dimensional ...
PUM
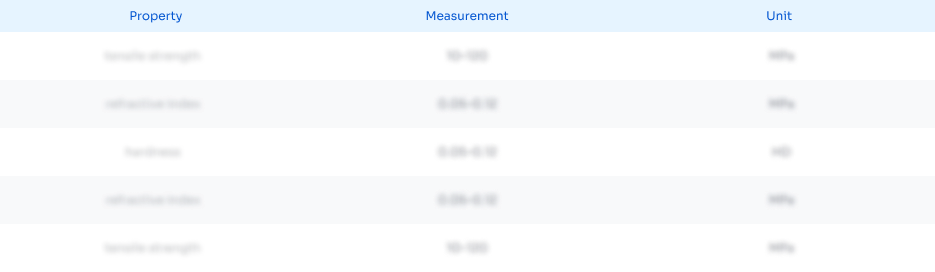
Abstract
Description
Claims
Application Information

- R&D
- Intellectual Property
- Life Sciences
- Materials
- Tech Scout
- Unparalleled Data Quality
- Higher Quality Content
- 60% Fewer Hallucinations
Browse by: Latest US Patents, China's latest patents, Technical Efficacy Thesaurus, Application Domain, Technology Topic, Popular Technical Reports.
© 2025 PatSnap. All rights reserved.Legal|Privacy policy|Modern Slavery Act Transparency Statement|Sitemap|About US| Contact US: help@patsnap.com