Construction method of fabricated steel mesh integrated composite wall
A construction method and composite wall technology, applied in the direction of walls, formwork/formwork/work frame connectors, building components, etc., can solve the problems of multiple processes, high comprehensive cost, and long construction period, so as to reduce waste of resources, The effect of reducing construction pollution and reducing labor costs
- Summary
- Abstract
- Description
- Claims
- Application Information
AI Technical Summary
Problems solved by technology
Method used
Examples
Embodiment 1
[0034] A construction method for a prefabricated steel mesh integrated composite wall, specifically comprising the following steps:
[0035] ⑴, accessories installation: install angle iron accessories around the wall;
[0036] ⑵. Keel installation: install special-shaped keels, which are arranged at vertical intervals, so that they are fixed together with angle irons up and down, and the distance between two special-shaped keels is 60cm;
[0037] ⑶. Steel mesh installation: Fix the steel mesh with screws on both sides of the special-shaped keel. When the length of the steel mesh is not enough, it needs to be extended and widened to connect the steel mesh. The specific method of extending and widening is binding with iron wire or connecting with C-shaped nails;
[0038] ⑷, wiring: drainage and wires inside the steel mesh;
[0039] ⑸. Fix the formwork: Fix the formwork on both sides of the steel mesh for the first time. The height of the formwork should be 2.0 to 2.5. The speci...
Embodiment 2
[0045] A construction method for a prefabricated steel mesh integrated composite wall, specifically comprising the following steps:
[0046] ⑴, accessories installation: install angle iron accessories around the wall;
[0047] ⑵. Keel installation: install special-shaped keels, which are arranged at vertical intervals, so that they are fixed together with angle irons up and down, and the distance between two special-shaped keels is 70cm;
[0048] ⑶. Steel mesh installation: Fix the steel mesh with a butt welder on both sides of the special-shaped keel. When the length of the steel mesh is not enough, it needs to be extended and widened to connect the steel mesh. The specific method of extending and widening is binding with iron wire or connecting with C-shaped nails;
[0049] ⑷, wiring: drainage and wires inside the steel mesh;
[0050] ⑸. Fix the formwork: Fix the formwork on both sides of the steel mesh for the first time. The height of the formwork should be 2.0 to 2.5. Th...
Embodiment 3
[0056] A construction method for a prefabricated steel mesh integrated composite wall, specifically comprising the following steps:
[0057] ⑴, accessories installation: install angle iron accessories around the wall;
[0058] ⑵. Keel installation: install special-shaped keels, which are arranged vertically and at intervals, so that they are fixed together with angle irons up and down, and the distance between two special-shaped keels is 45cm;
[0059] ⑶. Steel mesh installation: Fix the steel mesh with a butt welder on both sides of the special-shaped keel. When the length of the steel mesh is not enough, it needs to be extended and widened to connect the steel mesh. The specific method of extending and widening is binding with iron wire or connecting with C-shaped nails;
[0060] ⑷, wiring: drainage and wires inside the steel mesh;
[0061] ⑸. Fix the formwork: Fix the formwork on both sides of the steel mesh for the first time. The height of the formwork should be 2.0 to 2...
PUM
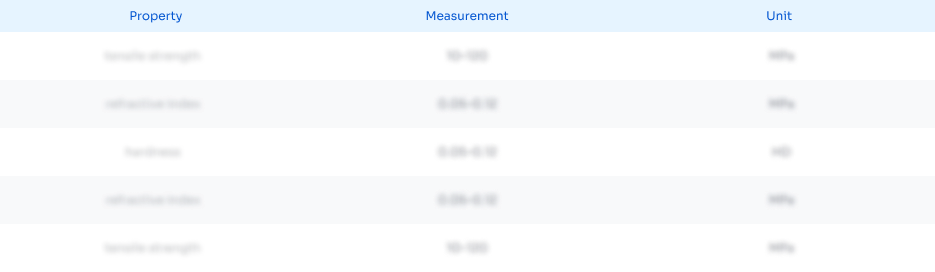
Abstract
Description
Claims
Application Information

- R&D
- Intellectual Property
- Life Sciences
- Materials
- Tech Scout
- Unparalleled Data Quality
- Higher Quality Content
- 60% Fewer Hallucinations
Browse by: Latest US Patents, China's latest patents, Technical Efficacy Thesaurus, Application Domain, Technology Topic, Popular Technical Reports.
© 2025 PatSnap. All rights reserved.Legal|Privacy policy|Modern Slavery Act Transparency Statement|Sitemap|About US| Contact US: help@patsnap.com