Method for removing calcium and magnesium from nickel, cobalt and manganese solution
A nickel-cobalt-manganese solution technology, which is applied in the field of nickel-cobalt hydrometallurgy, can solve the problems of calcium sulfate crystallization blocking the extraction tank and pipeline, the need for regular cleaning, and the difficulty of separation, etc., and achieves easy implementation, reduced impact, and simple process Effect
- Summary
- Abstract
- Description
- Claims
- Application Information
AI Technical Summary
Problems solved by technology
Method used
Image
Examples
Embodiment 1
[0024] The composition of the nickel-cobalt-manganese solution after iron removal in a certain factory is as follows:
[0025] element Al Fe Ca co Cr Cu Mg mn Ni Zn Composition / (g / L) 0.06 0.004 0.56 9.09 0.025 0.24 1.56 3.54 95.7 1.73
[0026] Take 500mL of the above solution, heat it to 30°C, add 3.78g of nickel fluoride according to the calculation of the theoretical amount of calcium and magnesium, and the time for calcium and magnesium removal is 6h. Calcium 0.01g / L, magnesium 0.02g / L.
Embodiment 2
[0028] The nickel-cobalt-manganese solution in a factory contains 0.54g / L of calcium and 2.34g / L of magnesium. Take 500mL of the solution and heat it to 70°C. According to the calculation of the theoretical amount of calcium and magnesium, 5.31g of nickel fluoride is added. The time for removing calcium and magnesium is 5 hours. Calcium-magnesium slag and calcium-magnesium-removed liquid were obtained by separation, and the calcium-magnesium-removed liquid contained 0.008 g / L of calcium and 0.016 g / L of magnesium.
Embodiment 3
[0030] A nickel-cobalt-manganese solution in a factory contains 0.57g / L of calcium and 2.03g / L of magnesium. Take 500mL of the solution and heat it to 90°C. Add 4.74g of cobalt fluoride according to the calculation of the theoretical amount of calcium and magnesium. The time for removing calcium and magnesium is 3 hours. Calcium-magnesium slag and calcium-magnesium-removed liquid were obtained by separation, and the calcium-magnesium-removed liquid contained 0.012 g / L of calcium and 0.018 g / L of magnesium.
PUM
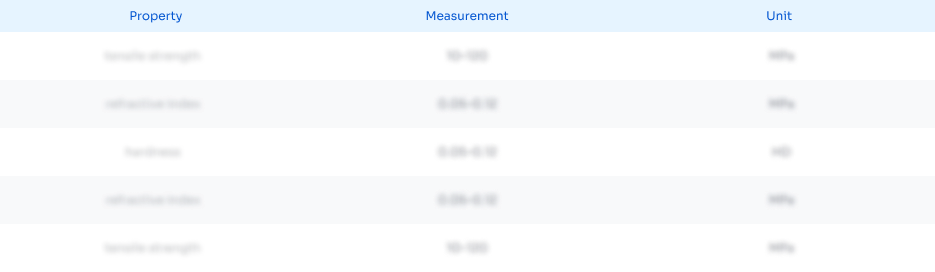
Abstract
Description
Claims
Application Information

- R&D Engineer
- R&D Manager
- IP Professional
- Industry Leading Data Capabilities
- Powerful AI technology
- Patent DNA Extraction
Browse by: Latest US Patents, China's latest patents, Technical Efficacy Thesaurus, Application Domain, Technology Topic, Popular Technical Reports.
© 2024 PatSnap. All rights reserved.Legal|Privacy policy|Modern Slavery Act Transparency Statement|Sitemap|About US| Contact US: help@patsnap.com