Laser wire fusing additive manufacturing titanium alloy component structure refining and isometric crystal converting method
A technology of additive manufacturing and laser melting, which is applied in the directions of additive manufacturing, additive processing, and process efficiency improvement. It can solve problems such as poor fatigue performance and coarse structure, and achieve the effect of compact structure and simplified path planning.
- Summary
- Abstract
- Description
- Claims
- Application Information
AI Technical Summary
Benefits of technology
Problems solved by technology
Method used
Image
Examples
Embodiment Construction
[0034] The present invention will be further described in detail below in conjunction with the accompanying drawings and specific embodiments.
[0035] The purpose of the present invention is to provide a simple method for microstructure refinement and equiaxed grain transformation of titanium alloy components manufactured by laser fuse additive manufacturing. The method couples the ultrasonic impact micro forging device with the laser fuse additive manufacturing device, The high-intensity ultrasonic energy field is introduced into the laser fuse additive manufacturing process, and at the same time exerts the interference effect of the ultrasonic energy field on the molten pool and the impact strengthening effect on the solid deposition layer, so as to improve the equiaxed grain transformation of titanium alloy components and refine the grain size. Particles and improve mechanical properties, solve the problem of coarse structure and poor fatigue performance of titanium alloy i...
PUM
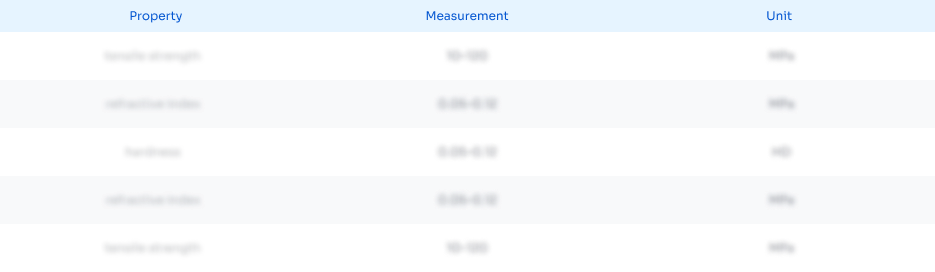
Abstract
Description
Claims
Application Information

- R&D
- Intellectual Property
- Life Sciences
- Materials
- Tech Scout
- Unparalleled Data Quality
- Higher Quality Content
- 60% Fewer Hallucinations
Browse by: Latest US Patents, China's latest patents, Technical Efficacy Thesaurus, Application Domain, Technology Topic, Popular Technical Reports.
© 2025 PatSnap. All rights reserved.Legal|Privacy policy|Modern Slavery Act Transparency Statement|Sitemap|About US| Contact US: help@patsnap.com