Temperature control system and method for injection mold
A temperature control system and temperature control method technology, applied in the field of injection mold control, can solve the problems of reducing production efficiency, temperature jump, temperature control instability, etc., to reduce concerns about production impact, stabilize temperature control, and simplify operation steps. Effect
- Summary
- Abstract
- Description
- Claims
- Application Information
AI Technical Summary
Problems solved by technology
Method used
Image
Examples
Embodiment 1
[0041] In order to solve the above problems, the mold can be heated up and down quickly, and the temperature control is stable, such as figure 1 and figure 2 As shown, the present invention proposes a temperature control system for injection molds, which is characterized in that it includes a temperature acquisition module, a main control module, a temperature control module and a heating device, wherein:
[0042] The temperature collection module is used to collect the temperature value of the mold cavity through a thermocouple;
[0043] The main control module is used to obtain the coefficient of the variable speed integral according to the adaptive PID algorithm when the deviation between the mold cavity temperature value and the set temperature value exceeds the set error range, thereby obtaining the duty cycle of the PWM wave, and generating a control Command to the temperature control module;
[0044] The temperature control module is used to adjust the on-off time (c...
Embodiment 2
[0089] like figure 2 Shown, the present invention also provides a kind of temperature control method for injection mold, it is characterized in that, comprises steps:
[0090] S1: collect the temperature value of the mold cavity;
[0091] S2: According to the actual temperature value, when the deviation between the mold cavity temperature value and the set temperature value exceeds the set error range, according to the adaptive PID algorithm, the coefficient of the variable speed integral is obtained, thereby obtaining the duty cycle of the PWM wave, and generating Control instruction;
[0092] S3: Adjust the on-off time according to the control command;
[0093] S4: heating the injection mold according to the on-off time.
[0094] Further, before the step S2, it also includes the steps of:
[0095] S20: Compensate the mold cavity temperature collected by the temperature acquisition module according to the thermistor in the cold junction compensation unit and the preset c...
Embodiment 3
[0111]In order to better understand a kind of temperature control system and method for injection mold described in the present invention, as image 3 and Figure 4 As shown, in this embodiment, a case that will occur during actual production is cited to describe the present invention in detail.
[0112] It is set to produce a round bowl-shaped lunch box mold. Before starting the mold production, the power module needs to be initialized first, and the 220V mains power is converted into common working voltages such as 9V, 5V, and 3.3V through a transformer, so that the power module can Provide safe working voltage for each module according to the working voltage of different modules to avoid machine damage caused by too low or too high voltage. At the same time, after completing the initialization of the power module, the staff also need to initialize the system setting module and other modules through the temperature setting unit, parameter setting unit and mode setting unit ...
PUM
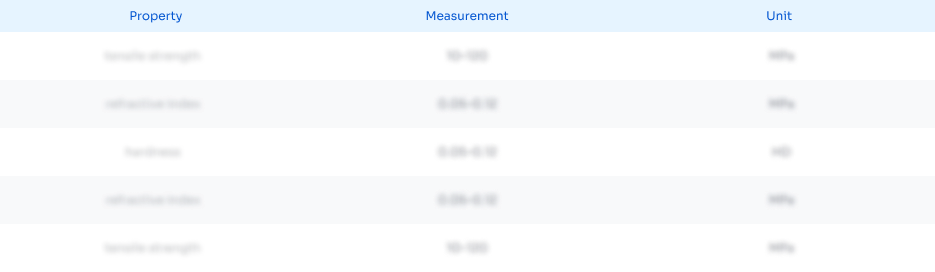
Abstract
Description
Claims
Application Information

- R&D
- Intellectual Property
- Life Sciences
- Materials
- Tech Scout
- Unparalleled Data Quality
- Higher Quality Content
- 60% Fewer Hallucinations
Browse by: Latest US Patents, China's latest patents, Technical Efficacy Thesaurus, Application Domain, Technology Topic, Popular Technical Reports.
© 2025 PatSnap. All rights reserved.Legal|Privacy policy|Modern Slavery Act Transparency Statement|Sitemap|About US| Contact US: help@patsnap.com