Low-power external rotor alternate current motor
An AC motor and outer rotor technology, used in the manufacture of motor generators, electric components, electrical components, etc., can solve the problems of axial concentricity skew deviation of the outer rotor shaft, scrapping, and inability to disassemble and repair.
- Summary
- Abstract
- Description
- Claims
- Application Information
AI Technical Summary
Problems solved by technology
Method used
Image
Examples
Embodiment Construction
[0010] The following examples and accompanying drawings describe the present invention in further detail: with reference to Figure 1 to Figure 3 , the present invention includes a stator 6, a stator fixing base 13, bearings 7, 8, an outer rotor 1, an outer rotor connecting end cover 10 and an outer rotor shaft 9, and the outer rotor 1 and the outer rotor connecting end cover 10 are manufactured separately Separate parts, the outer rotor 1 is adjacent to the outer rotor connecting end cover 10. The side of the cast aluminum ring 2 is formed with an attachment surface 3 and four concentric and evenly distributed screw holes 5 of the same specification, adjacent to the outer rotor connecting end cover 10 One side of the outer rotor is formed with a corresponding connecting surface 11 and four through holes 12 that are uniformly distributed concentrically, and there are four matching screws 4. The outer rotor shaft 9 and the outer rotor connecting end cover 10 are fixed concentric...
PUM
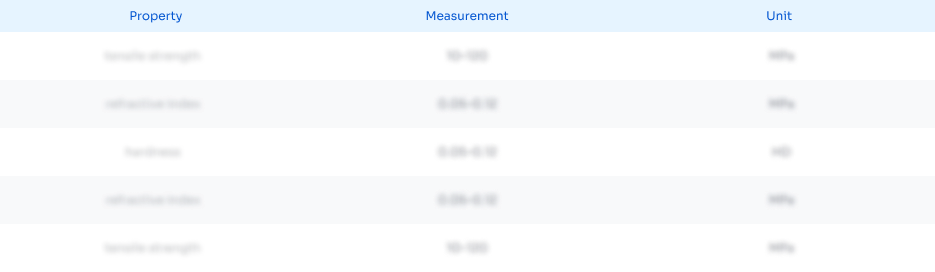
Abstract
Description
Claims
Application Information

- R&D Engineer
- R&D Manager
- IP Professional
- Industry Leading Data Capabilities
- Powerful AI technology
- Patent DNA Extraction
Browse by: Latest US Patents, China's latest patents, Technical Efficacy Thesaurus, Application Domain, Technology Topic, Popular Technical Reports.
© 2024 PatSnap. All rights reserved.Legal|Privacy policy|Modern Slavery Act Transparency Statement|Sitemap|About US| Contact US: help@patsnap.com