Semi-automatic loading and unloading bridge with route planning algorithm and control method
A path planning, loading and unloading bridge technology, applied in the field of control, can solve the problems of difficult loading and unloading of compartments, hidden compartments of ships, etc.
- Summary
- Abstract
- Description
- Claims
- Application Information
AI Technical Summary
Problems solved by technology
Method used
Image
Examples
Embodiment 1
[0031] Embodiment 1: see Figure 1-Figure 3 , a semi-automatic loading and unloading bridge with a path planning algorithm, which includes an outdoor UWB ultra-wideband cart wireless positioning device 1 for measuring the Y-axis coordinates of the cart defined in the system software; a position encoder installed on the motor shaft of the cart 6. It is used to measure the X coordinate of the car from the boarding position defined in the system software, and a set of laser ranging encoder is used as the position correction when the wheel slips; the encoder installed on the wire rope drum of the hoisting mechanism 7. It is used to measure the Z-axis coordinate of the lifting hook head starting from the ground. The loading and unloading bridge includes a support frame 12, a remote control device 2, an on-shore laser radar visual recognition device 3, an electronic anti-sway device 10, a ground control server 4, and an on-board PLC motion control system. The shaking device 10 is a...
Embodiment 2
[0032] Example 2: see Figure 1-Figure 3 , a semi-automatic loading and unloading bridge control method with path planning algorithm, the method comprises the following steps:
[0033] ①Path planning curve "boarding point" setting, A, cart initial position setting: the production operator sends the coordinates measured by the wireless positioning device to the ground control server in the transportation information system according to the position where the ship stops, and then the ground control The server sends it to the PLC motion control system on the machine to drive the cart to the designated position. B. The initial position setting of the trolley: the cab is parked at the position of the boarding platform, and there is a stop limit and position encoder detection of the trolley at this position. C. Lifting initial position setting: The lifting mechanism is at the upper stop limit position, which is detected by the lifting position encoder at the same time. The point whe...
PUM
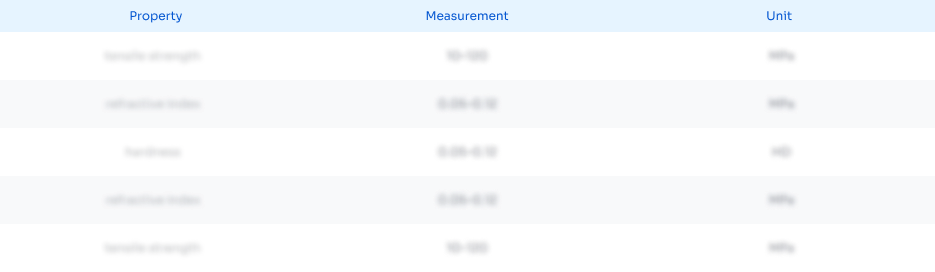
Abstract
Description
Claims
Application Information

- Generate Ideas
- Intellectual Property
- Life Sciences
- Materials
- Tech Scout
- Unparalleled Data Quality
- Higher Quality Content
- 60% Fewer Hallucinations
Browse by: Latest US Patents, China's latest patents, Technical Efficacy Thesaurus, Application Domain, Technology Topic, Popular Technical Reports.
© 2025 PatSnap. All rights reserved.Legal|Privacy policy|Modern Slavery Act Transparency Statement|Sitemap|About US| Contact US: help@patsnap.com