Synthesis process of favipiravir and intermediate thereof
A synthesis process and favipiravir technology are applied in the synthesis of favipiravir intermediate 6-fluoro-3-benzyloxy-2-pyrazinecarboxamide and the field of favipiravir synthesis, which can solve the problem of high cost , unfavorable to large-scale production and other problems, to achieve the effects of low cost, short reaction time and mild reaction conditions
- Summary
- Abstract
- Description
- Claims
- Application Information
AI Technical Summary
Problems solved by technology
Method used
Image
Examples
Embodiment 1
[0044] Embodiment 1: the preparation of compound III
[0045]
[0046] materials molecular weight Feeding amount molar weight Proportion 2-aminomalonamide 117 100g 0.85mol 1 40% glyoxal in water 58.01 149.4g 1.03mol 1.2 20% NaOH 40 220ml 1.11mol 1.3 6mol / l hydrochloric acid ethanol 1mol / L NaOH
[0047] In the reaction flask, add 220ml of 20% sodium hydroxide aqueous solution, cool to -10°C, and then add 100g of 2-aminomalonic acid diamide to suspend it in the solution. Then, 149.4 g of 40% glyoxal aqueous solution was added dropwise, and the addition was completed in about 40 minutes. After the addition was complete, the reaction mixture was stirred at -5°C for 1 hour, warmed to 22°C, and stirred for an additional 3 hours.
[0048] After the reaction was completed, it was cooled to below 5° C., and the reaction compound was adjusted to pH 12 by adding 1 mol / l sodium hydroxide and mad...
Embodiment 2
[0049] Embodiment 2: the preparation of compound IV
[0050]
[0051]
[0052]
[0053] In the reaction flask, add 100 g of compound III and 1 L of acetonitrile, and stir. Then add 199g of potassium carbonate, 25.8g of tetrabutylammonium iodide, and 135g of benzyl bromide in sequence, raise the temperature to 55-60°C, and react for 12-14h. The raw materials basically react completely.
[0054] After the reaction, add 1 L of water to the system, extract 1 L x 2 times with ethyl acetate, combine the organic phases, wash once with 1 L of water, and add anhydrous sodium sulfate to dry. Filtration, precipitation under reduced pressure to obtain oily substance IV: 153.3g, yield 93.1%
Embodiment 3
[0055]Embodiment 3: the preparation of compound V (Corning microchannel reactor, its module and structural diagram are as figure 1 shown)
[0056]
[0057] materials molecular weight Feeding amount molar weight Proportion Compound IV 229.09 10g 0.044mol 1 formic acid 90g Fluorine gas 40 2.1g 0.052mol 1.2 Nitrogen 28 18.9g
[0058] Refer to as figure 2 As shown in the flowchart, follow the steps below:
[0059] Compound IV was dissolved in formic acid solution, prepared to 10wt%, cooled to 5-10°C, and kept warm. The number is solution A, the system is about 100ml.
[0060] It is prepared into 10wt% sodium hydroxide solution, and placed at the outlet of the microchannel reactor to stir.
[0061] Lower the temperature of the microchannel reactor to 5-8°C in advance, and use the feed pump to simultaneously inject solution A (10wt%, 10g / min) and fluorine gas (10vol% of nitrogen, 2.1g / min) into the silicon carb...
PUM
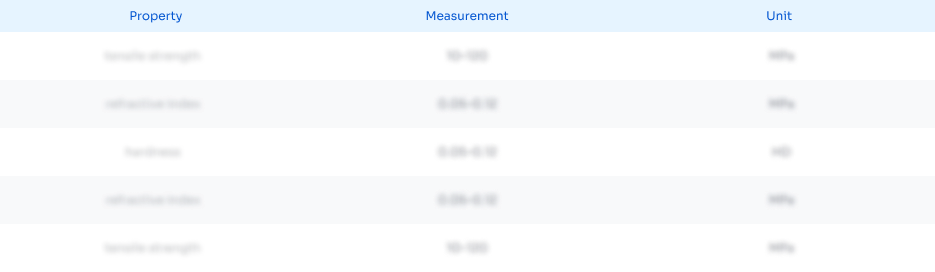
Abstract
Description
Claims
Application Information

- R&D Engineer
- R&D Manager
- IP Professional
- Industry Leading Data Capabilities
- Powerful AI technology
- Patent DNA Extraction
Browse by: Latest US Patents, China's latest patents, Technical Efficacy Thesaurus, Application Domain, Technology Topic, Popular Technical Reports.
© 2024 PatSnap. All rights reserved.Legal|Privacy policy|Modern Slavery Act Transparency Statement|Sitemap|About US| Contact US: help@patsnap.com