Veneer continuous tooth jointing machine
A tooth joint and veneer technology, which is applied in the field of wood processing, can solve the problems of low production efficiency, easy breakage of tooth joint interface, poor splicing effect, etc., and achieve good pressing effect, smooth movement and good tooth joint effect
- Summary
- Abstract
- Description
- Claims
- Application Information
AI Technical Summary
Problems solved by technology
Method used
Image
Examples
Embodiment 1
[0035] A single-board continuous tooth splicing machine, comprising a frame 11, a feeding mechanism 12, a comb tooth mechanism 13, a forward docking mechanism 14, a gluing mechanism 15, a pressing mechanism 16, and a rear transmission mechanism 17; There is a feeding mechanism 12, one side of the feeding mechanism 12 is provided with a comb mechanism 13, one side of the comb mechanism 13 is provided with a forward docking mechanism 14, a side of the forward docking mechanism 14 is provided with a gluing mechanism 15, and a side of the gluing mechanism 15 is provided There is a pressing mechanism 16, and a rear transmission mechanism 17 is provided on one side of the pressing mechanism 16.
[0036] The feeding mechanism 12 includes a feeding bracket 101, a cylinder I 102, a connecting plate I 103, a lower pressure roller I 104, a conveying roller I 105, and a motor I 106. The feeding bracket 101 is provided with a pair of cylinders I 102, and the head of the cylinder I 102 is provi...
Embodiment 2
[0046] Compared with the first embodiment, the difference is that: the forward docking mechanism 14 and the pressing mechanism 16 are provided with a docking adjustment mechanism. The docking adjustment mechanism includes a base beam 701, a slider II705, a guide rail II706, and a wire sleeve fixing Seat 707, screw sleeve 708, screw 709, screw bracket 7091, stop 7092, timing belt wheel 710, timing belt 711, motor Ⅳ 712, support block Ⅱ 713, butt adjustment bracket 714, butt adjustment cylinder 715, lower pressing block Ⅱ 716 The upper part of the base beam 701 is provided with a supporting block II 713, both ends of the supporting block II 713 are provided with a docking adjustment bracket 714, the docking adjustment bracket 714 is provided with a docking adjustment cylinder 715, and the head of the docking adjustment cylinder 715 is provided with a lower pressing block II 716; The bottom of the base beam 701 is provided with a slider II705, the bottom of the slider II705 is prov...
Embodiment 3
[0050] Compared with Embodiment 1, the difference is: the feeding mechanism 12 is provided with a 90° steering mechanism 2 on one side, and the 90° steering mechanism 2 is provided with a splicing machine 1 on one side, and the tail of the sizing mechanism 18 is connected by a conveyor belt for stacking Mechanism 3, in order to increase the utilization rate of veneers, small veneers are spliced horizontally by a splicing machine, and after a 90° turn, they enter the continuous gear splicing machine for longitudinal splicing.
PUM
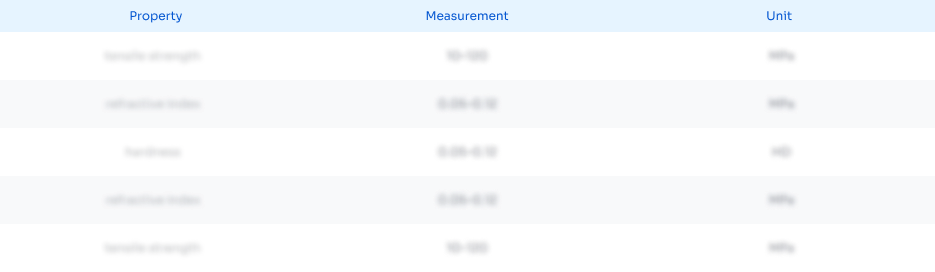
Abstract
Description
Claims
Application Information

- R&D Engineer
- R&D Manager
- IP Professional
- Industry Leading Data Capabilities
- Powerful AI technology
- Patent DNA Extraction
Browse by: Latest US Patents, China's latest patents, Technical Efficacy Thesaurus, Application Domain, Technology Topic, Popular Technical Reports.
© 2024 PatSnap. All rights reserved.Legal|Privacy policy|Modern Slavery Act Transparency Statement|Sitemap|About US| Contact US: help@patsnap.com